World's First Application of New In-Line Rail Hardening from Siemens Goes Commercial at Baotou
12/30/2014 - Siemens Metals Technologies has received notice from Baotou Iron & Steel (Group) Co. Ltd. that the in-line “Injector Dual-phase Rail Hardening” (Idrha+) achieved the expected performances for the rail R60 U75V gr.340 according to TB/T2344-2012 norm and has therefore entered the regular commercial production.
The system, contracted to Siemens in December 2012, is capable to improve the rail resistance to both wear and rolling contact fatigue, and was designed by Siemens Metals Technologies and Centro Sviluppo Materiali S.p.A. (RINA-CSM).
The grade U75V is one of the most widely produced rails for high-speed application. After head-hardening treatment with Idrha+ process, all the obtained mechanical and metallurgical characteristics of the rails exceed the values required by the applicable standards. In particular, the minimum values of UTS tensile strength and A% elongation are 1180 MPa and 10%, respectively. The measured values of hardness range from 340 to 400 Brinell HBW10/3000 at the surface of the rail head, and from 34 to 42 Rockwell HRC across the rail section, according to the applicable measuring protocol. R60 U75V gr.340 is the first rail in the world to be commercially processed through Idrha+, and is now in industrial production already at a rate of 15 pieces per hour with a 100-m standard length.
With a rail production capacity up to 1.36 million tons (record reached in 2009), Baotou is the largest rail manufacturer in the world. The first in-line Idrha+ system is installed in the rail rolling mill nr. 2, which has a yearly capacity of 400,000 metric tons and produces various sizes and grades of rails for domestic and export markets, according to the main international standards.
The design of the Idrha+ system by Siemens and Centro Sviluppo Materiali S.p.A. (RINA-CSM) is based on thermo-mechanical and metallurgical process models, and validated by experimental trials in a pilot plant. This allows the simulation of various cooling strategies for different grades of rail steel prior to the start of production, thus enabling run-up times to be shortened and nominal capacity to be attained faster while relevant performance parameters are fulfilled consistently and reliably.
The Idrha+ system allows for a unique flexibility of use and consistency of performance, thanks to the integration of a selective induction heating station, including powerful sequential spraying cooling modules with adaptive settings. The in-line installation grants a very high productivity with significant energy savings.
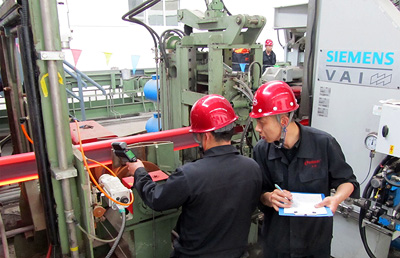
Pictured above: Hot tests of Idrha+ system at Baotou Iron & Steel.
The grade U75V is one of the most widely produced rails for high-speed application. After head-hardening treatment with Idrha+ process, all the obtained mechanical and metallurgical characteristics of the rails exceed the values required by the applicable standards. In particular, the minimum values of UTS tensile strength and A% elongation are 1180 MPa and 10%, respectively. The measured values of hardness range from 340 to 400 Brinell HBW10/3000 at the surface of the rail head, and from 34 to 42 Rockwell HRC across the rail section, according to the applicable measuring protocol. R60 U75V gr.340 is the first rail in the world to be commercially processed through Idrha+, and is now in industrial production already at a rate of 15 pieces per hour with a 100-m standard length.
With a rail production capacity up to 1.36 million tons (record reached in 2009), Baotou is the largest rail manufacturer in the world. The first in-line Idrha+ system is installed in the rail rolling mill nr. 2, which has a yearly capacity of 400,000 metric tons and produces various sizes and grades of rails for domestic and export markets, according to the main international standards.
The design of the Idrha+ system by Siemens and Centro Sviluppo Materiali S.p.A. (RINA-CSM) is based on thermo-mechanical and metallurgical process models, and validated by experimental trials in a pilot plant. This allows the simulation of various cooling strategies for different grades of rail steel prior to the start of production, thus enabling run-up times to be shortened and nominal capacity to be attained faster while relevant performance parameters are fulfilled consistently and reliably.
The Idrha+ system allows for a unique flexibility of use and consistency of performance, thanks to the integration of a selective induction heating station, including powerful sequential spraying cooling modules with adaptive settings. The in-line installation grants a very high productivity with significant energy savings.
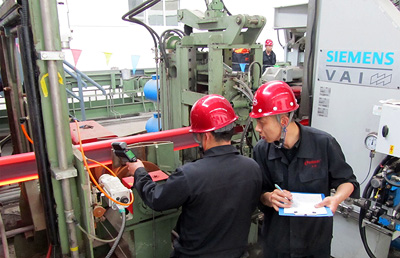
Pictured above: Hot tests of Idrha+ system at Baotou Iron & Steel.