Iron & Steel Technology
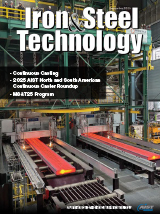
September Issue Now Online!
Continuous Casting
Special Features Include:Table of Contents
50
Investigation on Caster Breakout During Flying Tundish Change and Separation Plate Using Innovative Techniques at ArcelorMittal Dofasco’s No. 1 Continuous Caster
A caster breakout event occurred at ArcelorMittal Dofasco’s No. 1 Continuous Caster in proximity to a grade transition with a flying tundish change and separator plate. Practices of flying tundish changes and separator plates have been well-established to cast grades of different chemistries with minimal interruption to productivity. Hence, it was unusual that a breakout occurred, well below the mold, despite these practices and this specific grade transition being successful multi-ple times prior. This article discusses innovative tools and techniques for the extensive investigation carried out and pro-poses an explanation of the breakout event, supported through evidence in the autopsy.
60
Reduction of Surface Defects on Steel Pieces That Occur in the Early Stages of Casting
While scabs and longitudinal surface cracks of rolled products can occur during the rolling process, there are cases where surface cracks on billets do not disappear during the rolling process and remain. This article introduces efforts against the following surface cracks that appear during the continuous casting process, which occur at the initial casting stage at the bottom of oscillation valleys: (1) Short-stroke/high-cycle mold oscillation; (2) Optimization of mold dimple patterns; and (3) Improving responsiveness of mold level control.
68
Mold Powder Behavior in a Medium-Thickness High-Speed Slab Caster at Nucor Steel Gallatin
The development of practices on the medium-thickness high-speed caster at Nucor Steel Gallatin has continued with a focus on casting powder interactions in the mold with respect to powder mixing, heat removal and thermocouple behavior. The impact of mold plate thickness changes and mold water are also illustrated to highlight the impact on heat removal.
78
Study of Sheeting Behavior During Continuous Casting of Medium-Carbon Steels in a Thin-Slab Caster
Sheeting is a phenomenon observed in continuous casting that leads to large deviations in heat flux. Such large devia-tions can lead to loss of lubrication, resulting in sticker breakouts and quality issues.1 Ozgu et al.2 postulated that sheeting was attributed to cracking of the solid flux layer which eventually falls out, leaving behind a thin layer between the slab and the mold. Similar behavior was noted when casting medium-carbon steel grades (0.17–0.24%C) on a thin-slab caster. This article investigates the influence of various operational conditions on sheeting behavior. Mold flux composition was found to be the most influential on sheeting intensity. Various mold flux chemistries were studied to find mold flux with the least amount of sheeting. Of the powders investigated, the version with 5% zirconia addition was found to be most effective.
88
Advancing Induction Heating Technology for Sustainable Processing and Property Enhancement for Advanced High-Strength Sheet Steels
This project aims to advance the technology development related to the replacement of combustion heat for steel manu-facturing with electrified induction heating technology for sustainable steel processing. The current investigation involves a comparative study of the effects of simulated induction annealing versus conventional continuous annealing on the microstructure development and mechanical performance of third-generation advanced high-strength sheet steels. The project outcome is envisioned to help the industry, especially steel suppliers to automotive original equipment manufactur-ers, realize process energy and emission savings while maintaining or improving product performance, thereby facilitating the decarbonization of process heat and transitioning to electrified and low-carbon fuel energy sources in the steel indus-try.