ThyssenKrupp Steel Europe Modernizing Converter Plant, Waste Heat Boiler in Duisburg-Bruckhausen
07/08/2014 - ThyssenKrupp Steel Europe is modernizing its No. 2 converter and associated waste-heat boiler system in the Duisburg-Bruckhausen, Germany, steelmaking plant, one of the biggest in Europe.
The modernization work, under way since the beginning of June, involves an investment of around €21 million. “This project will improve energy efficiency and increase process reliability,” said Dr. Arnd Köfler, head of crude steel at ThyssenKrupp Steel Europe. “It will further enhance the quality of our products and ultimately benefit our customers.”
The first of two converters in oxygen steelmaking plant 1 was replaced over a year ago, also at a cost of around 20 million euros. Now it is the turn of converter 2. It’s another major logistical exercise: While production in converter 1 continues, around 1,000 specialists are working on two job sites to ensure a smooth rebuild. “We are removing the old equipment and installing the new while the neighboring converter operates as normal. Planning and organizing the whole operation including health & safety measures has been a huge challenge,” says Dr. Köfler.
Larger converter vessel increases process reliability and energy efficiency
The latest modernization mainly involves two units: the converter and the waste-heat boiler. The new converter vessel is one of the biggest of its kind worldwide, with a height of eleven meters and a width of 15 meters. Including bearing stands, converter platform, etc. the total weight of the steel structure is around 600 tons. Thanks to a new method of construction the new converter vessel will be significantly wider. With an unchanged charge weight of up to 400 tons, the inner volume of the converter has been increased by almost a fifth. The additional capacity will provide greater process reliability, as the steel bath will be at a lower level in the converter, reducing the possibility of steel spilling out of the mouth. Also, thanks to the larger reaction volume, more oxygen can be injected during the top-blowing process. As a result the escaping converter gas will have a higher carbon content, meaning that more process energy can be recovered in further process steps.
Special crane lifts boiler segments over shop roof
Directly above the work on the converter floor, four segments of the waste-heat boiler system are also being replaced. The over 50 meter long system of water pipes cools the converter off-gas from up to 1,800°C down to roughly 500°C, ready for dust removal. The steam produced in the process flows into the mill’s steam network, where it is converted into electricity or injected into the blast furnace. The cooled converter gas is cleaned and used as fuel for the reheating furnaces in the adjacent hot strip mill, benefiting functionality, energy efficiency and the environment.
The new boiler segments were made by the Essen-based equipment manufacturer Oschatz. They are up to 4.3 meters in diameter. The heaviest element weighs 50 tons, and together the four weigh 150 tons. As the waste-heat boiler has to be positioned roughly 20 meters above the converter opening, three of the four boiler segments will be lifted over the 70 meter high shop roof into the converter shop on the hook of a special crawler-mounted Wagenborg crane with a 140 meter boom positioned on the south side of the Duisburg-Bruckhausen melt shop.
Once the converter is closed down, every hour counts, so installation will be swift. Based on the experience gained last year, even less time has been allowed for the whole replacement. The new converter is scheduled to produce its first heat at the end of July.
Engineering and fabrication have been carried out by Düsseldorf-based SMS Siemag. Dismantling and installation are being handled by sister company ThyssenKrupp Mill Services & Systems under a contract from SMS Siemag. Project management is the responsibility of ThyssenKrupp Steel Europe’s “Technical services and energy” unit, which is coordinating work on the site in close cooperation with the production and maintenance departments.
Converters form the basis for steel production in Bruckhausen
The two converters in oxygen steelmaking plant 1 have been the basis for steel production in Duisburg-Bruckhausen since 1969. In the refractory-lined steel vessels pig iron is converted into crude steel with the addition of scrap and slag formers. At temperatures of up to 3,000 degrees impurities contained in the pig iron such as carbon and silicon are removed. 45 years of continuous operation and around 220,000 heats have left their marks on converter 2. Now it is being replaced. Together the two converters produce around five million tons of liquid steel per year.
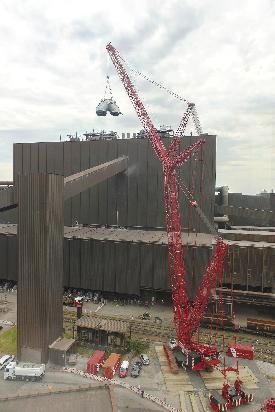
Pictured above: Spectacular lifting operation: A special crane moves a 50 ton boiler segment into a shop building of ThyssenKrupp Steel Europe for the modernization of converter 2 and associated waste-heat boiler system.
The first of two converters in oxygen steelmaking plant 1 was replaced over a year ago, also at a cost of around 20 million euros. Now it is the turn of converter 2. It’s another major logistical exercise: While production in converter 1 continues, around 1,000 specialists are working on two job sites to ensure a smooth rebuild. “We are removing the old equipment and installing the new while the neighboring converter operates as normal. Planning and organizing the whole operation including health & safety measures has been a huge challenge,” says Dr. Köfler.
Larger converter vessel increases process reliability and energy efficiency
The latest modernization mainly involves two units: the converter and the waste-heat boiler. The new converter vessel is one of the biggest of its kind worldwide, with a height of eleven meters and a width of 15 meters. Including bearing stands, converter platform, etc. the total weight of the steel structure is around 600 tons. Thanks to a new method of construction the new converter vessel will be significantly wider. With an unchanged charge weight of up to 400 tons, the inner volume of the converter has been increased by almost a fifth. The additional capacity will provide greater process reliability, as the steel bath will be at a lower level in the converter, reducing the possibility of steel spilling out of the mouth. Also, thanks to the larger reaction volume, more oxygen can be injected during the top-blowing process. As a result the escaping converter gas will have a higher carbon content, meaning that more process energy can be recovered in further process steps.
Special crane lifts boiler segments over shop roof
Directly above the work on the converter floor, four segments of the waste-heat boiler system are also being replaced. The over 50 meter long system of water pipes cools the converter off-gas from up to 1,800°C down to roughly 500°C, ready for dust removal. The steam produced in the process flows into the mill’s steam network, where it is converted into electricity or injected into the blast furnace. The cooled converter gas is cleaned and used as fuel for the reheating furnaces in the adjacent hot strip mill, benefiting functionality, energy efficiency and the environment.
The new boiler segments were made by the Essen-based equipment manufacturer Oschatz. They are up to 4.3 meters in diameter. The heaviest element weighs 50 tons, and together the four weigh 150 tons. As the waste-heat boiler has to be positioned roughly 20 meters above the converter opening, three of the four boiler segments will be lifted over the 70 meter high shop roof into the converter shop on the hook of a special crawler-mounted Wagenborg crane with a 140 meter boom positioned on the south side of the Duisburg-Bruckhausen melt shop.
Once the converter is closed down, every hour counts, so installation will be swift. Based on the experience gained last year, even less time has been allowed for the whole replacement. The new converter is scheduled to produce its first heat at the end of July.
Engineering and fabrication have been carried out by Düsseldorf-based SMS Siemag. Dismantling and installation are being handled by sister company ThyssenKrupp Mill Services & Systems under a contract from SMS Siemag. Project management is the responsibility of ThyssenKrupp Steel Europe’s “Technical services and energy” unit, which is coordinating work on the site in close cooperation with the production and maintenance departments.
Converters form the basis for steel production in Bruckhausen
The two converters in oxygen steelmaking plant 1 have been the basis for steel production in Duisburg-Bruckhausen since 1969. In the refractory-lined steel vessels pig iron is converted into crude steel with the addition of scrap and slag formers. At temperatures of up to 3,000 degrees impurities contained in the pig iron such as carbon and silicon are removed. 45 years of continuous operation and around 220,000 heats have left their marks on converter 2. Now it is being replaced. Together the two converters produce around five million tons of liquid steel per year.
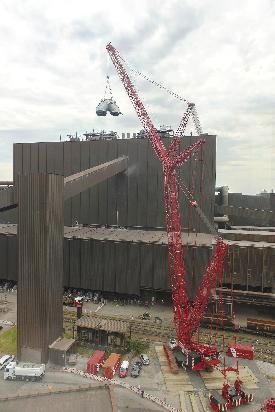
Pictured above: Spectacular lifting operation: A special crane moves a 50 ton boiler segment into a shop building of ThyssenKrupp Steel Europe for the modernization of converter 2 and associated waste-heat boiler system.