ThyssenKrupp Presents SteeloCare: The First Tinplate Monobloc Design Aerosol Can
05/23/2014 - In a technology alliance with press manufacturer Schuler and aerosol can former specialist Lanico, the packaging steel producer ThyssenKrupp Rasselstein is presenting an entirely newly designed tinplate aerosol can.
This product innovation “SteeloCare” features a completely monobloc look with excellent printing quality and surface feel, with seamless printed impression and without visible bottom fold.
Thanks to reduced wall thickness the new can reaches an empty weight close to the competing aluminum can. Dr. Reiner Sauer, Research Director at ThyssenKrupp Rasselstein, describes the progress of the innovative development this way: "The monobloc design aerosol can developed by Rasselstein makes aerosol cans made of packaging steel very attractive. In addition, they are very economical, since thanks to DWI they have very thin and pressure-stable can walls. Furthermore, the use of tools and machines is minimized. Since the packaging steel is coated on both sides with plastic (PET), this monobloc can has great corrosion stability combined with an appealing feel.
However, the elegant appearance of this modern aerosol package which may be used for toiletry, cosmetics as well as for food products, is just the beginning. More innovation and dynamics lie behind the materials used, the manufacturing process, and the economic and sustainability benefits for the entire value-creation chain. ThyssenKrupp Rasselstein, a subsidiary of ThyssenKrupp Steel Europe, is making a further optimized HF steel available especially for this application. The outstanding feature of this material innovation is its much-increased elongation — that is, its forming capacity — combined with a fineness characteristic otherwise only of especially hard steels; this produces an extremely even surface. The initial 0.190 mm thickness of the tinplate is reduced by about half, to between 0.100 mm and 0.090 mm. The first benefit is already clear here: the thinner wall thickness makes the empty can weigh comparable with competing models made of aluminum. Currently there are sample cans with body diameters of 45 and 58 mm.
Invisible to the end user are additional benefits of ThyssenKrupp Rasselstein's HF steel innovation: narrow tolerances during end forming reduce reworking and material loss, and the specially treated surface requires only an extremely thin coating application, which allows a largely mono-material recycling at the end of the cycle.
Thanks to coating with a similarly optimized PET film, which is laminated to the steel glue-free using special heat technology, there are also several benefits for the manufacturing and usage of this can innovation. The varnishing and drying steps of the conventional process are eliminated — and thus their machine and energy costs — and there is also new room to play with the coloration of and printing on the package. Last but not least, the plastic lamination is BPA-free, a strong argument in the especially sensitive market segments for personal care and food products.
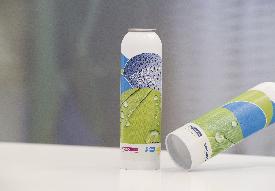
Pictured above: The entirely newly designed tinplate aerosol can SteeloCare.
Thanks to reduced wall thickness the new can reaches an empty weight close to the competing aluminum can. Dr. Reiner Sauer, Research Director at ThyssenKrupp Rasselstein, describes the progress of the innovative development this way: "The monobloc design aerosol can developed by Rasselstein makes aerosol cans made of packaging steel very attractive. In addition, they are very economical, since thanks to DWI they have very thin and pressure-stable can walls. Furthermore, the use of tools and machines is minimized. Since the packaging steel is coated on both sides with plastic (PET), this monobloc can has great corrosion stability combined with an appealing feel.
However, the elegant appearance of this modern aerosol package which may be used for toiletry, cosmetics as well as for food products, is just the beginning. More innovation and dynamics lie behind the materials used, the manufacturing process, and the economic and sustainability benefits for the entire value-creation chain. ThyssenKrupp Rasselstein, a subsidiary of ThyssenKrupp Steel Europe, is making a further optimized HF steel available especially for this application. The outstanding feature of this material innovation is its much-increased elongation — that is, its forming capacity — combined with a fineness characteristic otherwise only of especially hard steels; this produces an extremely even surface. The initial 0.190 mm thickness of the tinplate is reduced by about half, to between 0.100 mm and 0.090 mm. The first benefit is already clear here: the thinner wall thickness makes the empty can weigh comparable with competing models made of aluminum. Currently there are sample cans with body diameters of 45 and 58 mm.
Invisible to the end user are additional benefits of ThyssenKrupp Rasselstein's HF steel innovation: narrow tolerances during end forming reduce reworking and material loss, and the specially treated surface requires only an extremely thin coating application, which allows a largely mono-material recycling at the end of the cycle.
Thanks to coating with a similarly optimized PET film, which is laminated to the steel glue-free using special heat technology, there are also several benefits for the manufacturing and usage of this can innovation. The varnishing and drying steps of the conventional process are eliminated — and thus their machine and energy costs — and there is also new room to play with the coloration of and printing on the package. Last but not least, the plastic lamination is BPA-free, a strong argument in the especially sensitive market segments for personal care and food products.
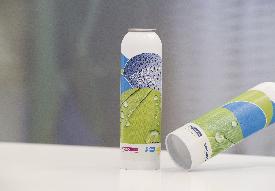
Pictured above: The entirely newly designed tinplate aerosol can SteeloCare.