SMS Siemag’s Converter-Vessel Changing Concept Successfully Implemented at PT Krakatau-Posco Company
06/19/2014 - PT Krakatau-Posco Company (PTKP), Indonesia, and SMS Siemag (www.sms-siemag.com), Germany, have successfully put into operation the efficient converter-vessel changing concept involving a 300 ton change-vessel converter, a changing car as well as highly effective environmental technology for the converter shop.
SMS Siemag developed the concept for the converter-vessel changing technology for PTKP and delivered the tilting gear unit for the converter, the changing car, which has a working load of 1,200 tons, and the complete X-Pact® electrical and automation package.
In the new PTKP plant, the latest generation of SMS Siemag's dry-type converter-gas dedusting technology has been deployed for the first time. This technology includes a gas conditioning tower and a dry-type electrostatic precipitator.
Lee Jung-Bae, project manager of the steelmaking plant at PTKP, is highly pleased with the new plant: “Using SMS Siemag's vessel changing concept was the right choice. It is the most economical solution.”
The converter-vessel changing concept provides for two blowing stands with permanently installed trunnion rings, three exchangeable converter vessels, a vessel changing car, a demolition and relining stand, a stand-by depositing station and a connecting trackway.
The converter-vessel changing car picks the worn converter up at the blowing stand and takes it to the demolition and relining stand. From there, the changing car moves to the depositing stand and collects the second converter vessel, which has already been relined, and takes it to the blowing stand.
Converter changing takes ten hours, i. e. it is accomplished within a regular maintenance shift at the steelworks. In its lower part, the changing car is equipped with a special lifting and turning manipu-lator, which enables the car to be turned through 90 degrees in order to reach the respective locations.
Dry-type converter-gas dedusting system with highliy effective environmental technology.The dust-laden flammable gas arising during the process is collected by the primary dust-collecting system above the opening of the converter and fed into the cleaning and recovery facilities.
The gas is cooled in the conditioning tower before cleaning is performed in the dry-type electrostatic precipitator. Here, the dust particles are efficiently separated. The electrostatic precipitators achieve a degree of separation of well over 99.8 percent. In the downstream spray-cooling tower, the cleaned gas is cooled in order to reduce its volume. Depending on the operating phase of the converter, the gas is either conducted to the flare or sent to the gas holder for intermediate storage. The gas-flow switch ensures reliable change-over. From the gas holder, the converter gas is fed to other consumption points in the works via a pressure-boosting station.
The dry-type electrostatic precipitator, with its low pressure loss, maintenance-friendly design and long service life, stands for low operating costs. Thanks to the high dust-extraction capacity, low residual dust contents can be attained and demanding environmental standards complied with. Both energy costs and CO2 emissions are significantly reduced, as the energy obtained from the flammable converter gas serves as a replacement for other energy sources.
PTKP, a joint venture between Pohang Iron & Steel Company (Posco), South Korea, and PT Krakatau Steel, Indonesia, is investing in a new integrated steel plant in Cilegon, West Java. The plant's annual production amounts to three million tons of steel. A second phase is planned to increase the production to six million tons.
West Java is the most heavily industrialized province in Indonesia.
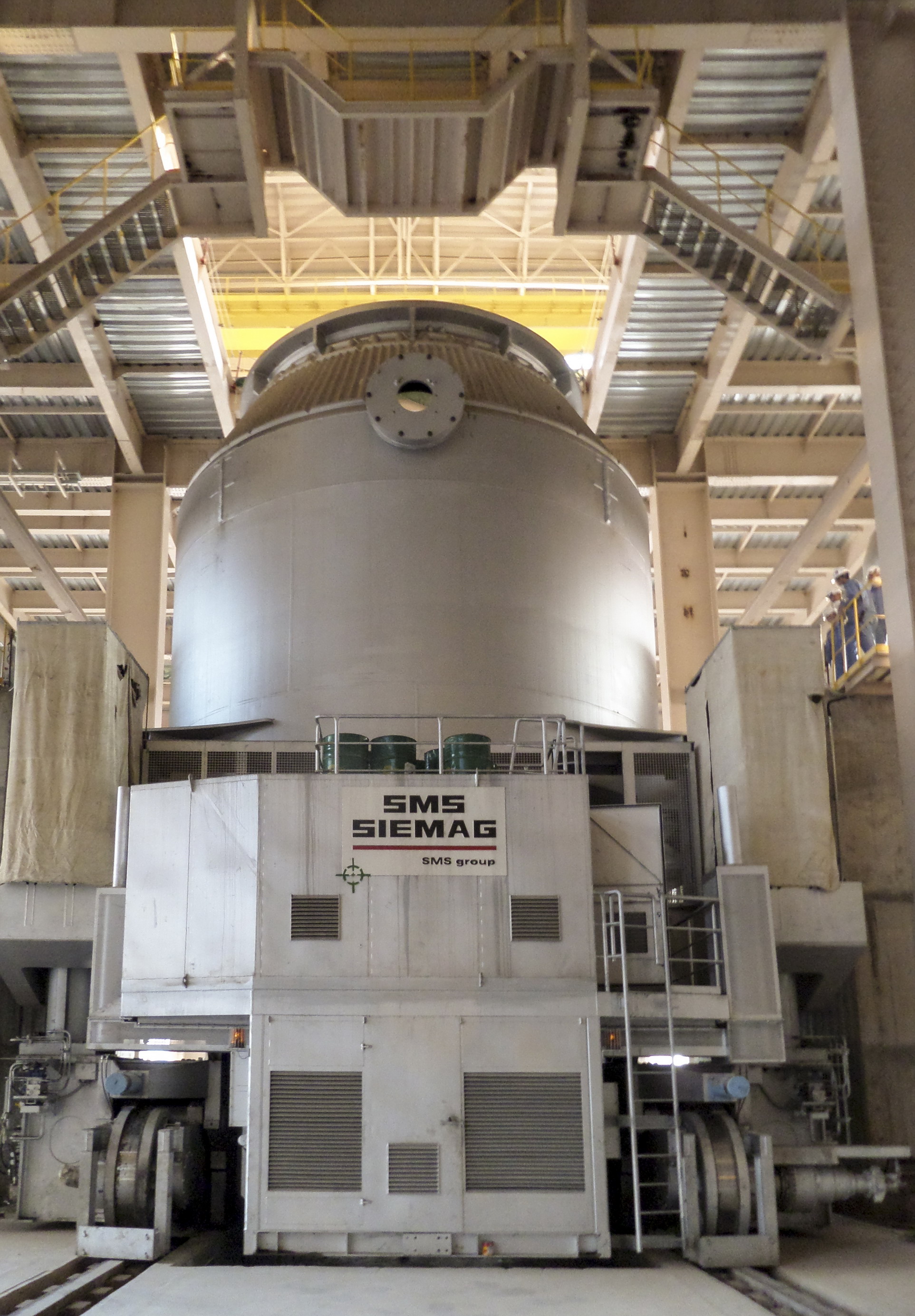
The converter vessel-changing car from SMS Siemag has a working load of 1,200 tons.
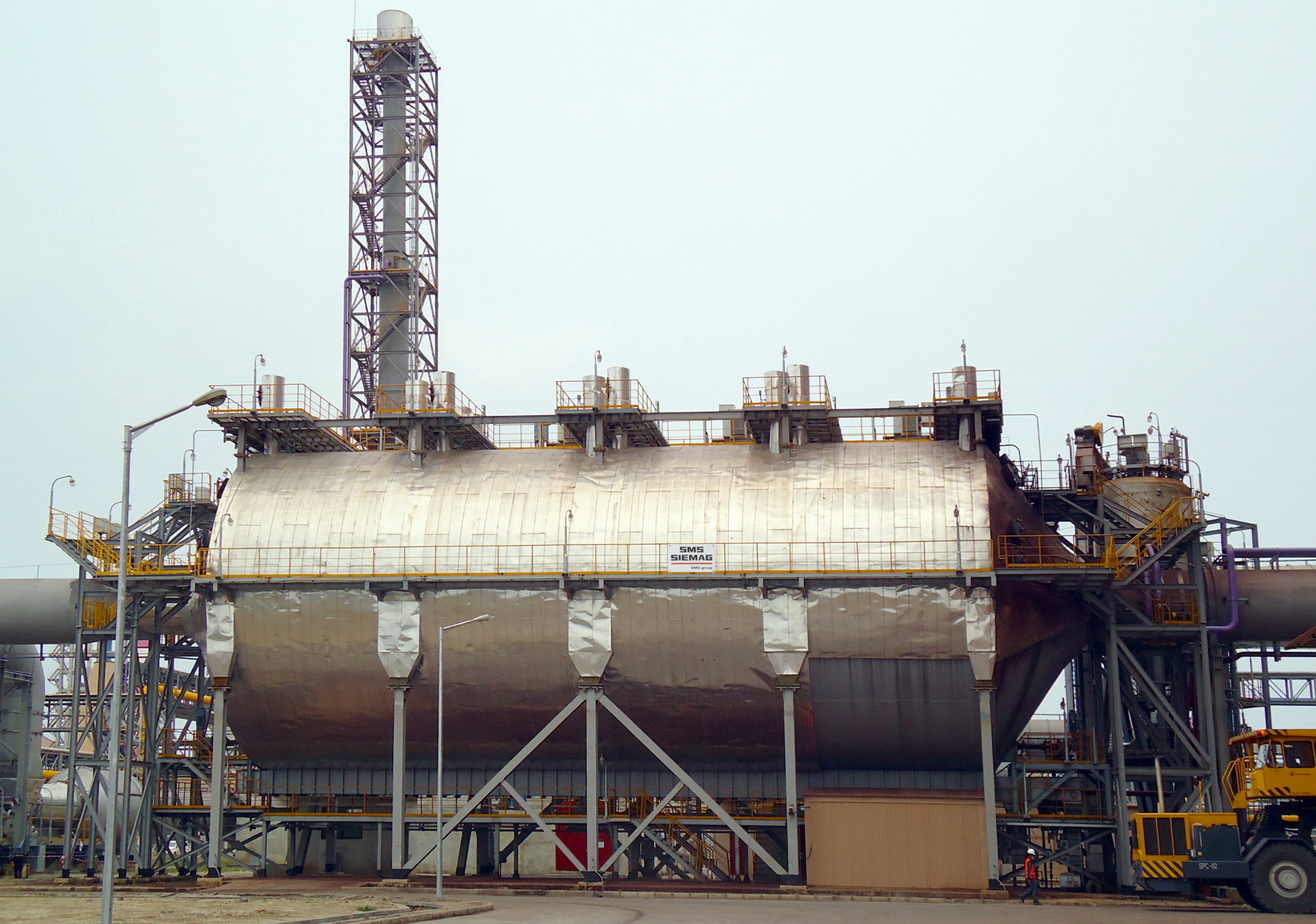
Highly effective environmental technology with the dry-type converter-gas dedusting system from SMS Siemag.
In the new PTKP plant, the latest generation of SMS Siemag's dry-type converter-gas dedusting technology has been deployed for the first time. This technology includes a gas conditioning tower and a dry-type electrostatic precipitator.
Lee Jung-Bae, project manager of the steelmaking plant at PTKP, is highly pleased with the new plant: “Using SMS Siemag's vessel changing concept was the right choice. It is the most economical solution.”
The converter-vessel changing concept provides for two blowing stands with permanently installed trunnion rings, three exchangeable converter vessels, a vessel changing car, a demolition and relining stand, a stand-by depositing station and a connecting trackway.
The converter-vessel changing car picks the worn converter up at the blowing stand and takes it to the demolition and relining stand. From there, the changing car moves to the depositing stand and collects the second converter vessel, which has already been relined, and takes it to the blowing stand.
Converter changing takes ten hours, i. e. it is accomplished within a regular maintenance shift at the steelworks. In its lower part, the changing car is equipped with a special lifting and turning manipu-lator, which enables the car to be turned through 90 degrees in order to reach the respective locations.
Dry-type converter-gas dedusting system with highliy effective environmental technology.The dust-laden flammable gas arising during the process is collected by the primary dust-collecting system above the opening of the converter and fed into the cleaning and recovery facilities.
The gas is cooled in the conditioning tower before cleaning is performed in the dry-type electrostatic precipitator. Here, the dust particles are efficiently separated. The electrostatic precipitators achieve a degree of separation of well over 99.8 percent. In the downstream spray-cooling tower, the cleaned gas is cooled in order to reduce its volume. Depending on the operating phase of the converter, the gas is either conducted to the flare or sent to the gas holder for intermediate storage. The gas-flow switch ensures reliable change-over. From the gas holder, the converter gas is fed to other consumption points in the works via a pressure-boosting station.
The dry-type electrostatic precipitator, with its low pressure loss, maintenance-friendly design and long service life, stands for low operating costs. Thanks to the high dust-extraction capacity, low residual dust contents can be attained and demanding environmental standards complied with. Both energy costs and CO2 emissions are significantly reduced, as the energy obtained from the flammable converter gas serves as a replacement for other energy sources.
PTKP, a joint venture between Pohang Iron & Steel Company (Posco), South Korea, and PT Krakatau Steel, Indonesia, is investing in a new integrated steel plant in Cilegon, West Java. The plant's annual production amounts to three million tons of steel. A second phase is planned to increase the production to six million tons.
West Java is the most heavily industrialized province in Indonesia.
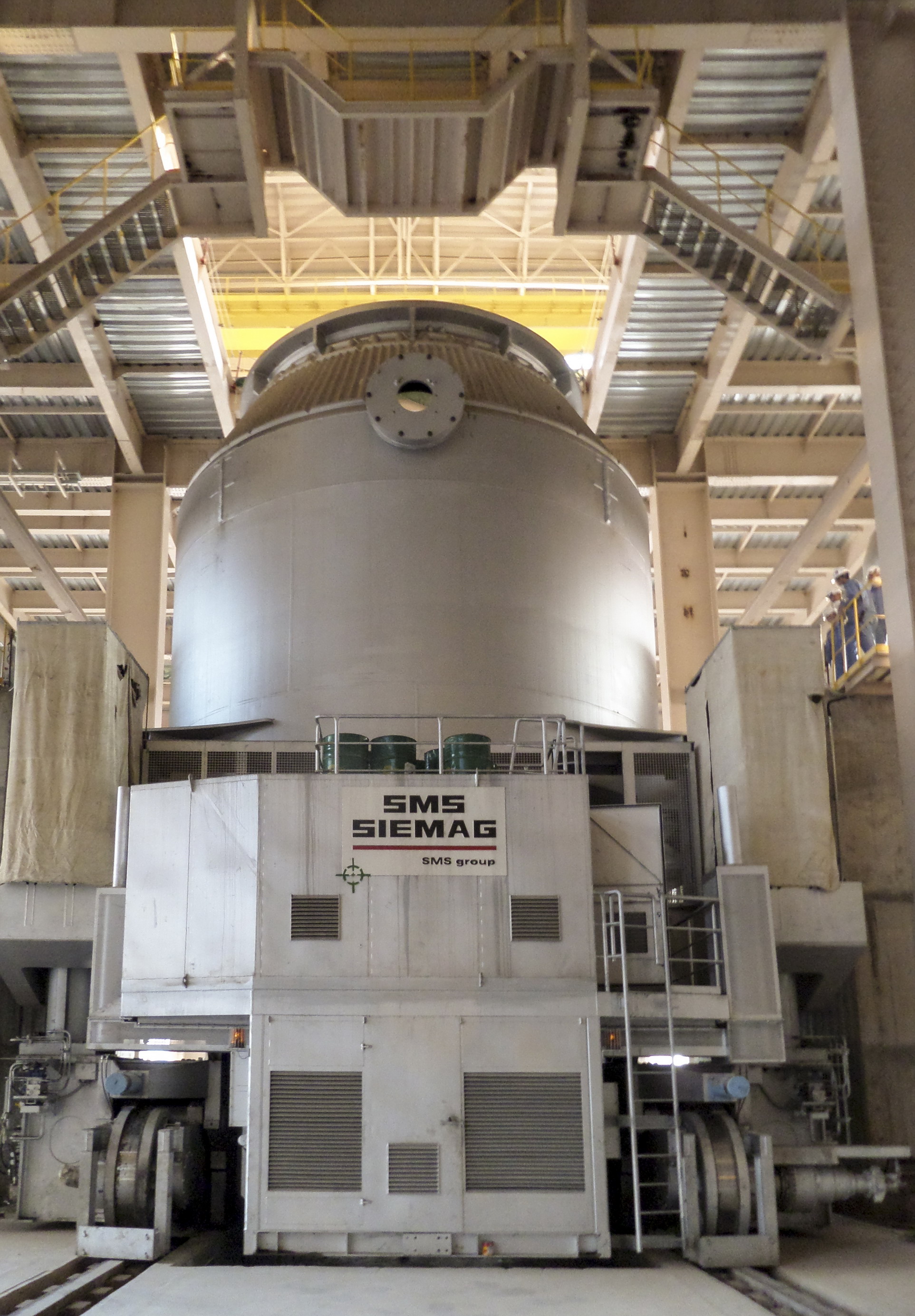
The converter vessel-changing car from SMS Siemag has a working load of 1,200 tons.
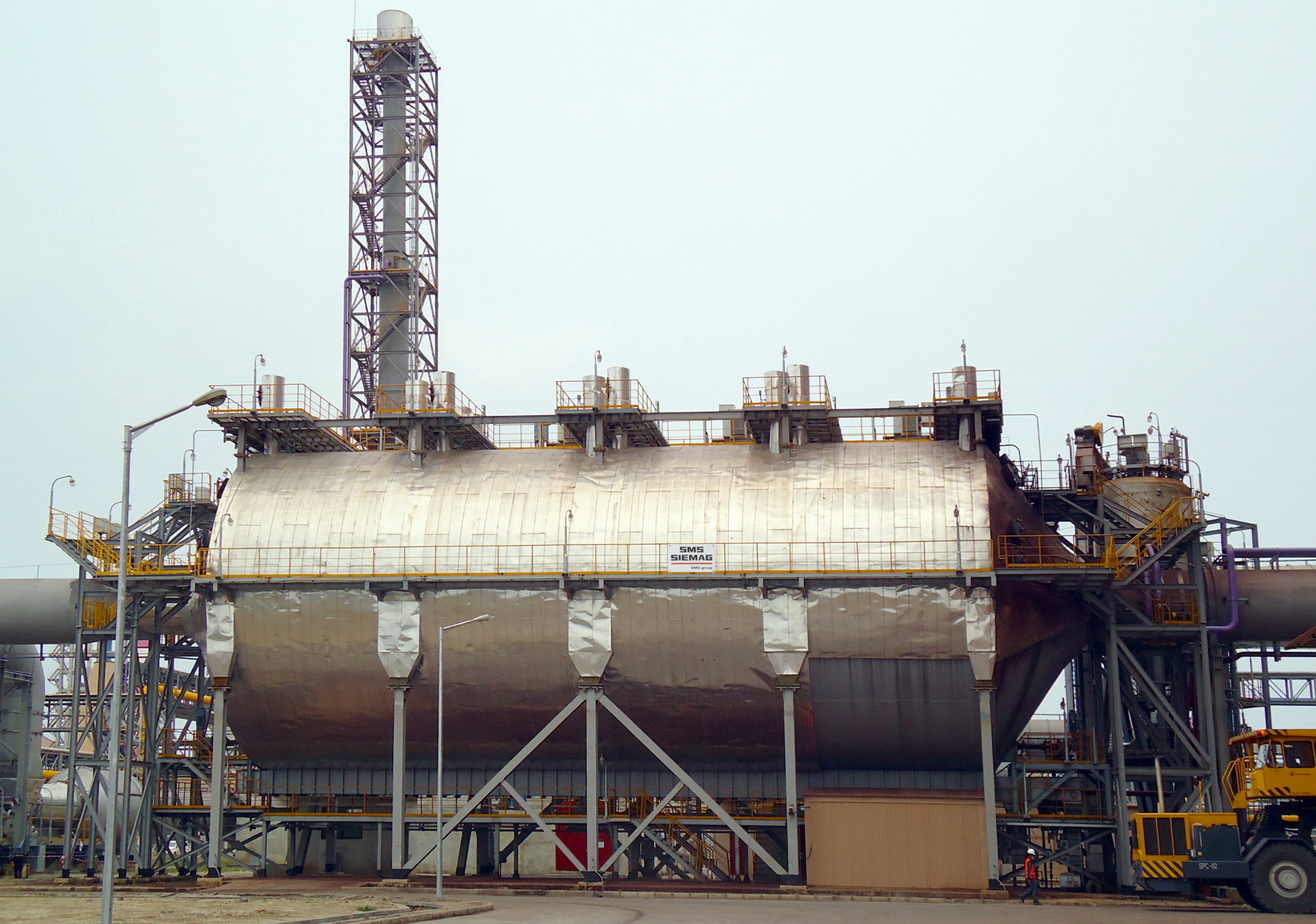
Highly effective environmental technology with the dry-type converter-gas dedusting system from SMS Siemag.