Siemens to Modernize Continuous Slab Caster for HKM
02/05/2014 - Hüttenwerke Krupp Mannesmann GmbH (HKM) has awarded Siemens Metals Technologies an order to modernize slab caster No. 3 in its Duisburg-Huckingen plant in Germany.
The project is intended to enhance the quality and product tolerances of the slabs produced, to widen the range of products, and to improve process stability, availability and safety at work. The casting plant will also be equipped with new basic and process automation, technology packages, such as DynaGap Soft Reduction, LevCon, DynaWidth and DynaFlex, and new safety equipment. The air mist secondary cooling will also be renewed to optimize the temperature control in order to produce high quality slabs. Modernization is scheduled to take place at the end of 2014 during a temporary plant shutdown.
The slab caster, which was delivered by a third-party supplier, has been in operation at HKM in Duisburg since 2000. Consequently, the supply of spare parts for much of the electrical equipment can no longer be guaranteed over the medium term. It is also becoming more difficult to meet the ever more stringent requirements for process stability and safety at work regulations. HKM has therefore decided to replace much of the electrical equipment with new Siemens systems. In the course of the project, the plant structure will also be adapted, redundancies installed, and the plant functionality extended. This will increase availability and improve product tolerances. Siemens will also fundamentally overhaul the existing air mist secondary cooling, and equip it with a DynaJet air mist system. This will enable HKM to further widen the range of high quality steel grades in its portfolio.
The modernization will also improve occupational health and safety in slab caster 3, not only to meet higher requirements but also exploit current technical possibilities. Risks in safety-relevant areas were assessed in advance of the project. A safety concept has been worked out and the safety equipment required for its implementation selected on the basis of these assessments.
Hüttenwerke Krupp Mannesmann GmbH (HKM) runs an integrated iron and steel mill at its Duisburg-Huckingen location. The works is divided into the subsections harbor, sinter plant, coking plant, blast furnace plant with two blast furnaces, and an LD basic oxygen furnace plant. Two round-steel continuous casters and three slab-casting facilities are in operation in the steel works. Each year, HKM produces more than 1,000 different grades of steel. It turns out some twelve percent of all the raw steel produced in Germany, and has a production capacity of around 5.6 million metric tons of steel per annum, making it one of the largest steel plants in Germany.
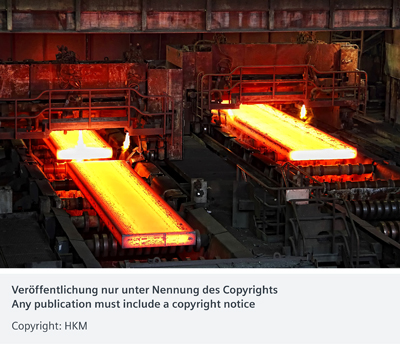
Pictured above: Slab caster No. 3 of HKM in Duisburg-Huckingen.
Siemens will modernize the casting plant by the end of 2014. (Copyright: HKM)
The slab caster, which was delivered by a third-party supplier, has been in operation at HKM in Duisburg since 2000. Consequently, the supply of spare parts for much of the electrical equipment can no longer be guaranteed over the medium term. It is also becoming more difficult to meet the ever more stringent requirements for process stability and safety at work regulations. HKM has therefore decided to replace much of the electrical equipment with new Siemens systems. In the course of the project, the plant structure will also be adapted, redundancies installed, and the plant functionality extended. This will increase availability and improve product tolerances. Siemens will also fundamentally overhaul the existing air mist secondary cooling, and equip it with a DynaJet air mist system. This will enable HKM to further widen the range of high quality steel grades in its portfolio.
The modernization will also improve occupational health and safety in slab caster 3, not only to meet higher requirements but also exploit current technical possibilities. Risks in safety-relevant areas were assessed in advance of the project. A safety concept has been worked out and the safety equipment required for its implementation selected on the basis of these assessments.
Hüttenwerke Krupp Mannesmann GmbH (HKM) runs an integrated iron and steel mill at its Duisburg-Huckingen location. The works is divided into the subsections harbor, sinter plant, coking plant, blast furnace plant with two blast furnaces, and an LD basic oxygen furnace plant. Two round-steel continuous casters and three slab-casting facilities are in operation in the steel works. Each year, HKM produces more than 1,000 different grades of steel. It turns out some twelve percent of all the raw steel produced in Germany, and has a production capacity of around 5.6 million metric tons of steel per annum, making it one of the largest steel plants in Germany.