Siemens Storage Logistics System Accepted by ArcelorMittal Eisenhüttenstadt
04/16/2014 - Steel producer ArcelorMittal Eisenhüttenstadt GmbH has issued Siemens Metals Technologies with the acceptance certificate for the new storage logistics system in its finishing department.
The Simetal Siloc logistics system now provides the company with a precise picture of its stock at all times and the over 40,000 slabs that pass through the slab storage each year. It not only enhances the composition of the stacks of slabs, but also automates logging of manual restacking operations. Simetal Siloc thus improves workflows and simplifies stock control. Cycle times have also been reduced because the slabs can be fed to the rolling mills at a higher temperature.
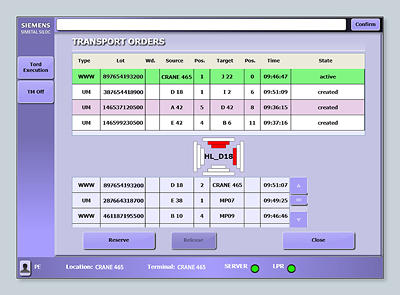
Navigation support for crane operators: The bar icons in the center indicate the current location of the crane. They are used to navigate to the center of the location and disappear when the crane is centered. ArcelorMittal Eisenhüttenstadt uses the Simetal Siloc storage logistics system from Siemens in its finishing department.
Dr. Ralf Bösler, Primary CEO at ArcelorMittal Eisenhüttenstadt GmbH, explained, "The new Siemens system, above all, meets future requirements for the planned modification and optimization of the technological and logistic processes in our company. The advanced strategies for storing and retrieving the slabs provide a good basis in particular."
ArcelorMittal is the world's largest steel producer and a global supplier of high-quality steel products. In Eisenhüttenstadt, in the German state of Brandenburg, the main products are high-quality, coated flat steels for the automotive industry, together with steel products for domestic appliances and the construction industry. The new Simetal Siloc storage logistics system from Siemens is part of a program to modernize the automation, and thereby increase the efficiency of hot strip production.
In the finishing department of the converter steel plant of ArcelorMittal Eisenhüttenstadt, slabs and blooms are accepted, inspected, transported, stored, processed according to scheduling and quality specifications, prepared for further processing in the hot rolling mill, and finally finished for dispatch. The plant personnel have to constantly coordinate the movements of twelve cranes, various storage areas, a number of roller tables, trolleys, inspection tables, heat recovery and the slitting and cross-cutting stations. Planning in the finishing department was previously done manually and independently of the higher-level planning processes. This resulted in a large number of restacking operations in all storage areas.
The new storage logistics system takes its instructions from the higher-level production planning system (PPS), the material tracking system (MVS) and the dispatch system. Simetal Siloc coordinates the work of the individual systems in the finishing department in line with the instructions of the material accepted. For example, the crane operator receives automatically generated transport orders on the terminal in his cab, which ensure optimum composition of the stacks of slabs. Simetal Siloc applies its own safety rules to ensure the stability of the stacks and protect the slabs from damage. The crane operator can also perform unscheduled restacking operations manually. These are then automatically registered by the system and entered in the database which is always up to date, allowing all material movements to be visualized.
The expandable, modular system is based on the Simatic IT and Simetal Siloc product platform. It provides a large number of organizational and commercial metrics in the form of clear graphics and tabular evaluations. For example, it can show how many crane movements have been made per shift for any category of slab, so that the time and cost for each operation can be calculated exactly.
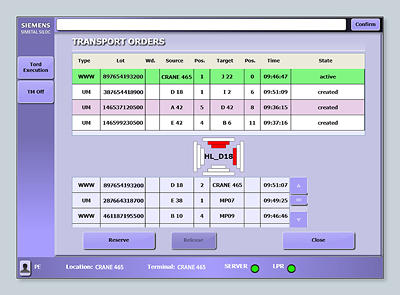
Navigation support for crane operators: The bar icons in the center indicate the current location of the crane. They are used to navigate to the center of the location and disappear when the crane is centered. ArcelorMittal Eisenhüttenstadt uses the Simetal Siloc storage logistics system from Siemens in its finishing department.
Dr. Ralf Bösler, Primary CEO at ArcelorMittal Eisenhüttenstadt GmbH, explained, "The new Siemens system, above all, meets future requirements for the planned modification and optimization of the technological and logistic processes in our company. The advanced strategies for storing and retrieving the slabs provide a good basis in particular."
ArcelorMittal is the world's largest steel producer and a global supplier of high-quality steel products. In Eisenhüttenstadt, in the German state of Brandenburg, the main products are high-quality, coated flat steels for the automotive industry, together with steel products for domestic appliances and the construction industry. The new Simetal Siloc storage logistics system from Siemens is part of a program to modernize the automation, and thereby increase the efficiency of hot strip production.
In the finishing department of the converter steel plant of ArcelorMittal Eisenhüttenstadt, slabs and blooms are accepted, inspected, transported, stored, processed according to scheduling and quality specifications, prepared for further processing in the hot rolling mill, and finally finished for dispatch. The plant personnel have to constantly coordinate the movements of twelve cranes, various storage areas, a number of roller tables, trolleys, inspection tables, heat recovery and the slitting and cross-cutting stations. Planning in the finishing department was previously done manually and independently of the higher-level planning processes. This resulted in a large number of restacking operations in all storage areas.
The new storage logistics system takes its instructions from the higher-level production planning system (PPS), the material tracking system (MVS) and the dispatch system. Simetal Siloc coordinates the work of the individual systems in the finishing department in line with the instructions of the material accepted. For example, the crane operator receives automatically generated transport orders on the terminal in his cab, which ensure optimum composition of the stacks of slabs. Simetal Siloc applies its own safety rules to ensure the stability of the stacks and protect the slabs from damage. The crane operator can also perform unscheduled restacking operations manually. These are then automatically registered by the system and entered in the database which is always up to date, allowing all material movements to be visualized.
The expandable, modular system is based on the Simatic IT and Simetal Siloc product platform. It provides a large number of organizational and commercial metrics in the form of clear graphics and tabular evaluations. For example, it can show how many crane movements have been made per shift for any category of slab, so that the time and cost for each operation can be calculated exactly.