Siemens Offers Solution for Generating Steam from EAF Off-Gases
11/15/2013 - Siemens Metals Technologies has developed a system for recovering heat from the hot off-gases of electric arc furnaces.
The thermal energy that was previously discharged unused to the environment is now used to generate steam. The steam can be put to good use in other processes in the steel works or in the generation of electricity. The system has a modular structure and can be dimensioned for the amount of heat to be recovered and integrated into the existing exhaust gas cooling system. To maximize the amount of steam obtained, it can substitute the complete conventional off-gas cooling system in the electric steel plant. A possible saving of 22.5 kilowatt hours per metric ton of steel in the specific use of energy was proven in a Turkish steel mill. If the generated steam is used to preheat the feed water in the plant's in-house power station, the annual savings potential amounts to 45,000 metric tons of coal.
In order to cut running costs or to fulfill environmental regulations, more and more operators of electric steel mills are banking on improving the energy efficiency of their plants. Although the electric steel production route based on scrap recycling has a much lower specific energy requirement than steel production from iron ore, it is nevertheless an energy-intensive process. Depending on the method of operation, up to one-third of the energy used by an electric arc furnace is lost through off-gases. The sensible heat of the exhaust gases is usually discharged unused to the environment through the water and air cooling systems.
Temperatures of up to 1,800 °C prevail in the exhaust gas stream. To make these considerable amounts of energy suitable for use, Siemens has developed a steam generation system that can be integrated into the existing off-gas cooling system of the arc furnace or can replace it entirely. The system consists of a boiler including steam drum, piping, water tanks, pump groups for feed and boiler water, and the associated sensors. A group of feed water pumps supplies the boiler with the necessary water and ensures the required pressure. To increase its recovery performance, the system can be equipped with a feed water preheating process called an "economizer". This economizer heats the water almost to the boiling point before feeding it into the steam drum on the boiler.
To separate the heat from the off-gas of the electric arc furnace as efficiently as possible, the new Siemens system has diverse nested radiation and convection heating surfaces. The water is fed to the heating surfaces through distribution pipes with the aid of recirculation pump groups. The amount of water fed depends on the different pipe geometries and the heat load of the respective sections. A correspondingly adapted recirculation ratio ensures safe, reliable and cost-effective operation of the boiler system. A certain amount of the boiler water evaporates during every circulation cycle between the steam drum and the heated surfaces. The resulting steam bubbles are then separated from the water inside the steam drum. A buffer storage can be optionally installed to balance out steam production, which is uneven due to the production process.
The heat recovery system from Siemens was specially conceived for the tough ambient conditions in the steel mill. Large amounts of dust and corrosive components in the exhaust gas must be dealt with as well as changing temperatures and amounts of the off-gas. Moreover, the system is equipped with the required safety facilities to comply with the Pressure Equipment Directive. It has a modular structure and can be adapted to differing requirements in each plant, thus facilitating the modernization of existing systems. Plant operators can choose between using the energy recovered in the form of steam directly or, for example, to generate electrical energy in steam turbines.
Installation of an energy recovery system in the exhaust gas system of an EAF with a tapping weight of 190 metric tons was analyzed within the scope of a feasibility study in a Turkish steel mill. The system was conceived for feed water preheating in the plant's own coal-fired power station. The continuous 50 bar(a) high-pressure steam production enables an annual saving of about 45,000 metric tons of coal in the power station. A power output of five megawatts (electrical) could be achieved if the steam were used directly to generate electricity. This corresponds to a reduction in the specific energy requirement of 22.5 kilowatt hours per metric ton of liquid steel.
Pictured below: Heat recovery system from Siemens:
The thermal energy recovered from the hot exhaust gases of electric arc furnaces is used to generate steam.
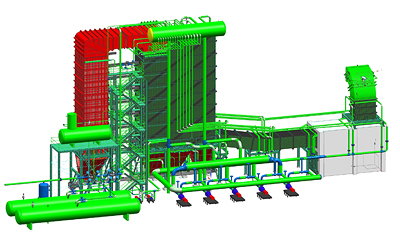
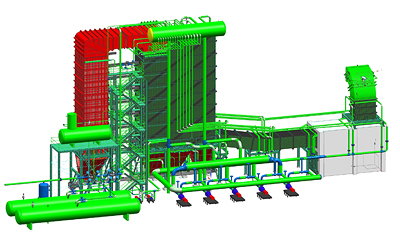
In order to cut running costs or to fulfill environmental regulations, more and more operators of electric steel mills are banking on improving the energy efficiency of their plants. Although the electric steel production route based on scrap recycling has a much lower specific energy requirement than steel production from iron ore, it is nevertheless an energy-intensive process. Depending on the method of operation, up to one-third of the energy used by an electric arc furnace is lost through off-gases. The sensible heat of the exhaust gases is usually discharged unused to the environment through the water and air cooling systems.
Temperatures of up to 1,800 °C prevail in the exhaust gas stream. To make these considerable amounts of energy suitable for use, Siemens has developed a steam generation system that can be integrated into the existing off-gas cooling system of the arc furnace or can replace it entirely. The system consists of a boiler including steam drum, piping, water tanks, pump groups for feed and boiler water, and the associated sensors. A group of feed water pumps supplies the boiler with the necessary water and ensures the required pressure. To increase its recovery performance, the system can be equipped with a feed water preheating process called an "economizer". This economizer heats the water almost to the boiling point before feeding it into the steam drum on the boiler.
To separate the heat from the off-gas of the electric arc furnace as efficiently as possible, the new Siemens system has diverse nested radiation and convection heating surfaces. The water is fed to the heating surfaces through distribution pipes with the aid of recirculation pump groups. The amount of water fed depends on the different pipe geometries and the heat load of the respective sections. A correspondingly adapted recirculation ratio ensures safe, reliable and cost-effective operation of the boiler system. A certain amount of the boiler water evaporates during every circulation cycle between the steam drum and the heated surfaces. The resulting steam bubbles are then separated from the water inside the steam drum. A buffer storage can be optionally installed to balance out steam production, which is uneven due to the production process.
The heat recovery system from Siemens was specially conceived for the tough ambient conditions in the steel mill. Large amounts of dust and corrosive components in the exhaust gas must be dealt with as well as changing temperatures and amounts of the off-gas. Moreover, the system is equipped with the required safety facilities to comply with the Pressure Equipment Directive. It has a modular structure and can be adapted to differing requirements in each plant, thus facilitating the modernization of existing systems. Plant operators can choose between using the energy recovered in the form of steam directly or, for example, to generate electrical energy in steam turbines.
Installation of an energy recovery system in the exhaust gas system of an EAF with a tapping weight of 190 metric tons was analyzed within the scope of a feasibility study in a Turkish steel mill. The system was conceived for feed water preheating in the plant's own coal-fired power station. The continuous 50 bar(a) high-pressure steam production enables an annual saving of about 45,000 metric tons of coal in the power station. A power output of five megawatts (electrical) could be achieved if the steam were used directly to generate electricity. This corresponds to a reduction in the specific energy requirement of 22.5 kilowatt hours per metric ton of liquid steel.