Siemens Management System Cuts Energy Costs of Electrostatic Precipitators in Steel Mills
12/17/2014 - With Precon, Siemens Metals Technologies is offering steel works operators an energy management system for electrostatic precipitators in dedusting plants.
The system includes components for data recording and processing, operator control and monitoring devices, and special software for controlling the precipitators. This enables the operation of the electrostatic precipitators to be matched optimally to the actual operating state of the converter. Depending on the environment and the type of electrostatic precipitator used, the energy consumption can be reduced by between 30–50%. The first Precon systems are in operation in a European steel plant. With the same dedusting performance, the precipitators there are saving more than 60% of their electrical energy consumption. The system typically pays back within one year, and can be retrofitted in existing plants without any additional shutdowns.
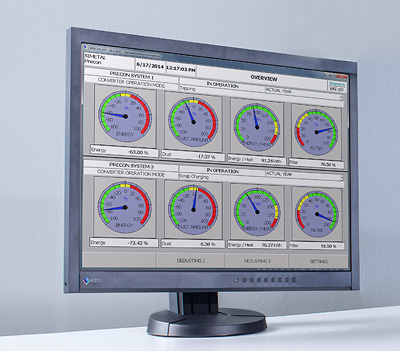
Pictured above: Overview of important operating data of
electrostatic precipitators in a European steel plant.
With a constant collection performance, Precon from Siemens is
reducing the electrical energy consumption there by more than 60%.
The electrostatic precipitator forms the heart of primary dedusting plants in steel works. It can remove around 99% of the dust from converter offgases. There is a direct voltage of up to 65 kilovolts between the discharge and collection electrodes. Depending on the size of the plant, the energy consumption varies between 1.4 and 2.1 kilowatt hours per metric ton of tapped steel. Therefore electrostatic precipitators are a major cost factor. The precipitators are usually operated so that dust concentration limits can be reliably maintained. However, as the dust emissions at the converter fluctuate widely in time, this operation practice is not in line with demand, and simply leads to higher operating costs.
Precon takes into account the various operating states of the converter throughout the complete cycle, and regulates the energy use of the precipitator to match current process conditions. This is achieved by precisely monitoring the power consumption of each individual precipitation field, and by a special software to evaluate all the relevant process data. On this basis, the high-voltage supplies to the precipitation fields can be controlled and optimized. The system includes pre-tested hardware, a Siemens Nanobox industrial PC, and an integrated programmable logic controller for communication with the high-voltage components of the precipitators. A touch panel facilitates user-friendly operation of Precon. If necessary, the system can be quickly switched from normal to optimized operation. There is no difficulty in retrofitting it in existing plants, and this can be done without any additional plant shutdown. A test system for determining the potential savings of a precipitation plant is also available.
For further information on solutions for steelworks, rolling mills and processing lines, see www.siemens.com/metals.
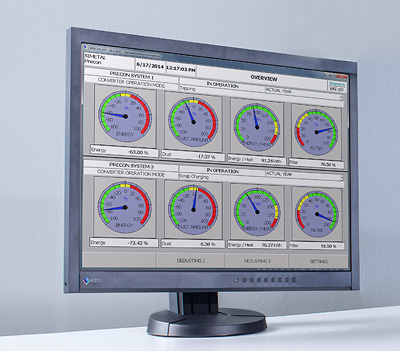
Pictured above: Overview of important operating data of
electrostatic precipitators in a European steel plant.
With a constant collection performance, Precon from Siemens is
reducing the electrical energy consumption there by more than 60%.
The electrostatic precipitator forms the heart of primary dedusting plants in steel works. It can remove around 99% of the dust from converter offgases. There is a direct voltage of up to 65 kilovolts between the discharge and collection electrodes. Depending on the size of the plant, the energy consumption varies between 1.4 and 2.1 kilowatt hours per metric ton of tapped steel. Therefore electrostatic precipitators are a major cost factor. The precipitators are usually operated so that dust concentration limits can be reliably maintained. However, as the dust emissions at the converter fluctuate widely in time, this operation practice is not in line with demand, and simply leads to higher operating costs.
Precon takes into account the various operating states of the converter throughout the complete cycle, and regulates the energy use of the precipitator to match current process conditions. This is achieved by precisely monitoring the power consumption of each individual precipitation field, and by a special software to evaluate all the relevant process data. On this basis, the high-voltage supplies to the precipitation fields can be controlled and optimized. The system includes pre-tested hardware, a Siemens Nanobox industrial PC, and an integrated programmable logic controller for communication with the high-voltage components of the precipitators. A touch panel facilitates user-friendly operation of Precon. If necessary, the system can be quickly switched from normal to optimized operation. There is no difficulty in retrofitting it in existing plants, and this can be done without any additional plant shutdown. A test system for determining the potential savings of a precipitation plant is also available.
For further information on solutions for steelworks, rolling mills and processing lines, see www.siemens.com/metals.