Siemens Jet Process Boosts Flexibility of Raw Material Use in Converter Steelmaking
11/29/2013 - With its Jet Process, Siemens Metals Technologies offers a solution for operating converters with up to 100% scrap and sponge iron.
This enables operators of melt shops to respond to raw material supply bottlenecks and exploit short-term price fluctuations. The solution consists of a bottom-blowing converter that makes it possible to blow in oxygen, lime and coal through bottom tuyeres and of a hot blast top lance for feeding additional energy into the steel bath. The Jet Process can either be implemented as a new installation or retrofitted in existing plants in a modular fashion.
Falling prices for scrap and direct reduced iron (sponge iron) as well as pressure from public authorities to reduce CO2 emissions offer stimuli for operators of integrated steel works to increase the share of scrap and sponge iron in the converter steel plant. Due to increasing price volatility, it has also become necessary to be able to flexibly adjust amounts of scrap and sponge iron to the respective market situation. A higher share of scrap or sponge iron calls for a supply of additional energy to maintain the temperature of the steel bath.
To fulfill these requirements, Siemens has developed a converter with bottom-blowing equipment and a hot blast lance. Oxygen, lime or coal can be fed into the steel bath with the aid of bottom tuyeres jets. Additionally, a top lance is used to blow a hot blast enriched to up to 40 percent of oxygen and a temperature of around 1,300 °C onto the bath. As a result of the high temperature, the speed of sound and the volume of the hot blast are high. This leads to excellent mixing, almost complete combustion of CO from the bath and optimum transfer of the heat generated in post combustion to the steel bath. A pebble heater with an energy efficiency of more than 95 percent is used to create the hot blast. Furthermore, the converter is equipped with a cooling stack to fully exploit the remaining thermal energy of the exhaust gas.
The bottom-blowing converter offers even more advantages. The oxygen bottom jets act as cutting torches, for example, enabling even large pieces of scrap to be melted with greater ease than in a conventional converter. Blowing in lime powder accelerates slag formation and desulfurization, thus improving process control. Bottom blowing also ensures a lower share of iron and iron oxide in the slag and lower slag volume in total, reducing evaporation of iron and crucially increasing the converter's yield and thus its profitability. The injected volume of coal can be varied within a wide scope. This permits easy and fast adjustment of the raw material composition to current market prices.
The Jet Process is particularly suitable for use in regions where scrap or sponge iron are relatively cheap compared to hot metal. It can also be used to circumvent bottlenecks in the availability of hot metal, either due to a planned production expansion, temporary unavailability of a blast furnace or because of production restrictions resulting from emission constraints imposed by authorities. The Jet Process has been successfully in operation at an Asian steel works since mid-2013.
Bottom-blowing converters with hot blast technology are part of the Siemens portfolio for special converters, offering steel producers greater flexibility in the use of raw materials, in particular if rates of scrap or sponge iron are high. Shares of up to 100 percent can be processed with these converters, much more than in conventional LD (BOF) converters. The special converters therefore close the gap between conventional converters and the electric steel production route.
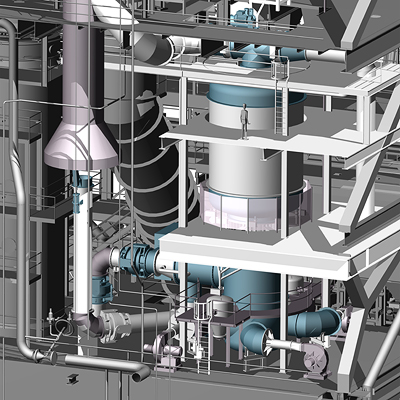
The Siemens Jet Process increases the flexibility of raw material selection on the converter.
Oxygen, lime and coal are blown in through bottom tuyeres
and a top lance blows hot jet onto the bath.
This results in excellent mixing and optimal use of the blown-in coal.
Falling prices for scrap and direct reduced iron (sponge iron) as well as pressure from public authorities to reduce CO2 emissions offer stimuli for operators of integrated steel works to increase the share of scrap and sponge iron in the converter steel plant. Due to increasing price volatility, it has also become necessary to be able to flexibly adjust amounts of scrap and sponge iron to the respective market situation. A higher share of scrap or sponge iron calls for a supply of additional energy to maintain the temperature of the steel bath.
To fulfill these requirements, Siemens has developed a converter with bottom-blowing equipment and a hot blast lance. Oxygen, lime or coal can be fed into the steel bath with the aid of bottom tuyeres jets. Additionally, a top lance is used to blow a hot blast enriched to up to 40 percent of oxygen and a temperature of around 1,300 °C onto the bath. As a result of the high temperature, the speed of sound and the volume of the hot blast are high. This leads to excellent mixing, almost complete combustion of CO from the bath and optimum transfer of the heat generated in post combustion to the steel bath. A pebble heater with an energy efficiency of more than 95 percent is used to create the hot blast. Furthermore, the converter is equipped with a cooling stack to fully exploit the remaining thermal energy of the exhaust gas.
The bottom-blowing converter offers even more advantages. The oxygen bottom jets act as cutting torches, for example, enabling even large pieces of scrap to be melted with greater ease than in a conventional converter. Blowing in lime powder accelerates slag formation and desulfurization, thus improving process control. Bottom blowing also ensures a lower share of iron and iron oxide in the slag and lower slag volume in total, reducing evaporation of iron and crucially increasing the converter's yield and thus its profitability. The injected volume of coal can be varied within a wide scope. This permits easy and fast adjustment of the raw material composition to current market prices.
The Jet Process is particularly suitable for use in regions where scrap or sponge iron are relatively cheap compared to hot metal. It can also be used to circumvent bottlenecks in the availability of hot metal, either due to a planned production expansion, temporary unavailability of a blast furnace or because of production restrictions resulting from emission constraints imposed by authorities. The Jet Process has been successfully in operation at an Asian steel works since mid-2013.
Bottom-blowing converters with hot blast technology are part of the Siemens portfolio for special converters, offering steel producers greater flexibility in the use of raw materials, in particular if rates of scrap or sponge iron are high. Shares of up to 100 percent can be processed with these converters, much more than in conventional LD (BOF) converters. The special converters therefore close the gap between conventional converters and the electric steel production route.