Siemens Continuous Caster Produces World's Thickest Stainless Steel Slabs At Posco
09/19/2013 - A single-strand continuous stainless steel slab caster capable of casting the world's thickest stainless steel slabs was brought into operation in July for Pohang Iron and Steel Co. Ltd. (Posco) in Pohang, South Korea.
Siemens Metals Technologies built the machine in Posco's stainless steel plant SSCP 4. It is designed to produce 700,000 metric tons of austenitic and ferritic steel slabs with thicknesses of up to 300 millimeters per annum. The new continuous casting plant expands Posco's capacity for producing high-quality stainless steels.
The continuous bow-type caster from Siemens is equipped with a straight smart mold. It has a machine radius of eleven meters and a metallurgical length of 26.9 meters. Slabs are cast with thicknesses of 250 and 300 millimeters in widths ranging from 800 to 1,650 millimeters. The casting speed can reach 1.1 meters per minute.
Siemens was responsible for the engineering, the supply of key components and technology packages, including the LevCon mold level control, the DynaFlex mold oscillator, and DynaWidth for setting the slab width. The strand is guided by Smart Segments. Thanks to DynaGap Soft Reduction 3D, it is possible to determine the position of the final solidification of the strand with high precision. This enables the roll gap to be controlled precisely and high internal slab quality to be obtained. A combination of the Dynacs 3D cooling module, DynaJet spray cooling and internally cooled I-Star rollers ensures efficient secondary cooling, an important prerequisite for achieving slabs with a high-quality surface. The scope of supplies and services from Siemens also included the complete basic (level 1) and process automation (level 2) of the casting plant as well as advisory services for construction and commissioning.
Continuous stainless-steel slab caster Siemens at Posco in Pohang, Korea.
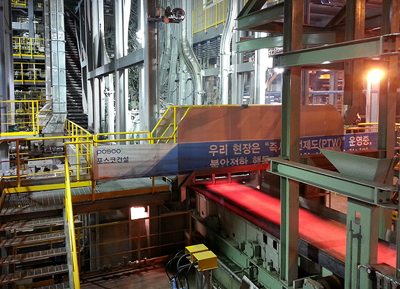
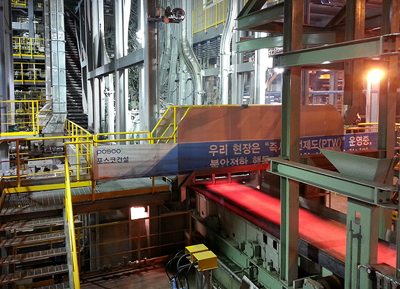
The continuous bow-type caster from Siemens is equipped with a straight smart mold. It has a machine radius of eleven meters and a metallurgical length of 26.9 meters. Slabs are cast with thicknesses of 250 and 300 millimeters in widths ranging from 800 to 1,650 millimeters. The casting speed can reach 1.1 meters per minute.
Siemens was responsible for the engineering, the supply of key components and technology packages, including the LevCon mold level control, the DynaFlex mold oscillator, and DynaWidth for setting the slab width. The strand is guided by Smart Segments. Thanks to DynaGap Soft Reduction 3D, it is possible to determine the position of the final solidification of the strand with high precision. This enables the roll gap to be controlled precisely and high internal slab quality to be obtained. A combination of the Dynacs 3D cooling module, DynaJet spray cooling and internally cooled I-Star rollers ensures efficient secondary cooling, an important prerequisite for achieving slabs with a high-quality surface. The scope of supplies and services from Siemens also included the complete basic (level 1) and process automation (level 2) of the casting plant as well as advisory services for construction and commissioning.