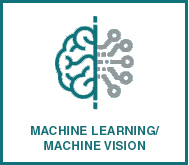 | | MACHINE LEARNINGMachine learning (ML) has myriad applications in steel. This article begins with a gentle introduction that situates ML with other forms of mathematical modeling. After establishing the basic principles of ML, modern use cases of ML within the steel sector are identified and presented. A GENTLE INTRODUCTION TO MACHINE LEARNINGMachine learning (ML) refers to a broad category of computational methods used for extracting patterns from data.1 Unlike traditional computer programs, ML methods can identify patterns that are not explicitly programmed in their code. Engineers can leverage these patterns to identify causal relationships that affect production, explain past production issues, and optimize process parameters to reduce scrap and improve end-of-line quality.
To understand how ML works, consider the following core concepts: Process: A series of steps, often involving physical equipment, that produces a product. Data: Historical or live measurements relating to a process, often taken from physical equipment. Domain knowledge: High-level information about a process that need not be reflected in data. This knowledge is high level in the sense that engineers who build and operate processes are clearly experts in their fields. But even the best engineer cannot immediately estimate mechanical or magnetic properties in real time, while taking into account the dozens (if not hundreds) of factors that affect it. A mathematical model of the process, however, is ideally suited for such a task.
ML uses historical data to build a mathematical model of a process (Fig. 1). Consider the use case of optimizing mechanical properties. The mill produces data that can be stored in the format of a table. Each row corresponds to a product. Three columns contain yield strength, tensile strength and elongation measurements; denote these as y. The others contain alloy composition measurements, meltshop parameters and rolling mill setpoints; denote these as x. ML can use this table to “learn” a multi-variate function y = f (x). The model f is statistical in nature; it is extracted from data by analyzing high-dimensional correlations. A good model should represent known (and potentially unknown) physical relationships that drive the process.
This highlights a critical assumption. The data should reflect the natural variation of the process. Measurements should contain common operating regimes and cover the majority of product types. ML strives to extract a function f that best describes the process; naturally, its effectiveness is limited by the quality of the data.
HOW DOES AN ML MODEL DIFFER FROM A CONVENTIONAL ONE? Conventional models (Fig. 2) are built on first principles and often focus on specific phenomena. They describe an idealized world, where all variables can be accounted for. In contrast, ML models learn from site-specific historical production data. They can take into account individual factors for a mill, discovering (potentially unknown) relationships. As such, ML models may identify new effects and highlight insights that only arise when considering an end-to-end view of a process.
WHAT CAN AN ENGINEER DO WITH AN ML MODEL OF A MILL? First, they can predict the mechanical properties of live production. This enables a workflow where meltshop operators can make cost-efficient decisions. Second, they can analyze and explain past production issues, such as “Why did a particular heat fail last week?” Finally, they can plan interventions. They can use the ML model to optimize a particular product to use less of an expensive alloy while meeting its mechanical property targets.
HOW IS ML DIFFERENT FROM STATISTICS? ML and statistics are closely related. ML builds upon statistics to find complex relationships in data, quantify the uncertainty in measurements, and identify linear and non-linear patterns. ML methods are often designed to scale to big and messy data sets, as well as to live data streaming settings.
HOW IS ML DIFFERENT FROM ARTIFICIAL INTELLIGENCE? Artificial intelligence (AI) can be thought of as “decisions based on ML-driven patterns.” For example, a self-driving car uses ML to detect stop signs in video data. An AI algorithm would then be the part that tells the car to stop based on detected stop signs. Another common application area is robotics, where AI methods iteratively decide how to move a robotic arm to accomplish a certain task.
MACHINE LEARNING AND STEELML is not new to steel. Since 1990, a type of ML model called “neural networks” has been leveraged at the process control level.2 These models are typically developed for specific use cases, such as blast furnace temperature optimization. The manufacturer of such units carefully pre-compute these models via laboratory testing and tune them for specific plants. They are operated in closed-loop control systems.
In contrast, statistical methods, such as linear regression, continue to be of use in the realm of Six Sigma and process optimization.3 These methods are typically available to plant engineers through various software tools. Engineers can apply them to a broad range of use cases based on their needs. This flexibility comes at a cost of low predictive power; as such, they are typically used for planning rather than in closed-loop systems.
How does modern machine learning fit into the picture today? Modern ML methods can be seen as combining the two approaches above. Engineers can capture complex relationships across a broad range of use cases. The same models can operate in both an outer-loop control system as well as production planning.
Modern ML comes with two costs. The first is computational power. While running ML software on desktop workstations and laptops is possible, there are significant benefits to leveraging cloud-based infrastructure to provide reliable, real-time computations. The second cost is specialization. Developing in-house ML expertise is challenging and expensive for steel companies, as recent workforce trends show a scarcity of qualified talent in this space.4
Modern ML research in “white-box” ML steer away from the black-box nature of conventional ML, such as “neural networks”, and drive toward presenting causal insights from data.5 Fig. 3 captures this transition.
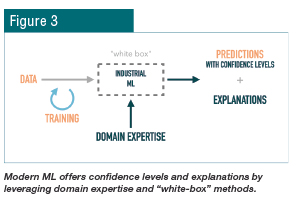 The development and application of modern ML presents new requirements. How to integrate domain knowledge and how to build trust are challenges of applying modern ML in practice. APPLICATIONSALLOY MINIMIZATION IN ELECTRIC ARC FURNACE (EAF) MILLS EAF mills work by melting scrap metal. This presents a specific challenge: how to best adapt to the (unknown) variation of alloys and residuals contained within the scrap. Meltshop operations are designed to repeatedly measure the chemical composition of each heat and gradually add additional alloys. As a result, unnecessary amounts of expensive alloys are often consumed to ensure final products hit their targets.
Modern ML can help guide decisions at this stage. ML can calculate the optimal amount of alloy to add to a heat, while taking into account how the product will be rolled. Fig. 4 visualizes this setup; note how the confidence intervals of each prediction matters. Meltshop operators that leverage these recommendations can obtain substantial savings in alloy consumption.
POWER LOSS MINIMIZATION IN ELECTRICAL STEEL Thousands of parameters affect the production of electrical steel. This presents a particular challenge when trying to diagnose the root cause of magnetic property deviations. With so many factors at play, a domain expert may struggle to narrow in on a set of factors that are worth studying.
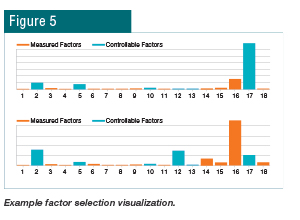 Fig. 5 shows how modern ML can represent the relative impact of multiple factors on a pair of targets. This highlights the ability of such methods to automatically identify (expected and unexpected) factors that influence magnetic properties. With modern ML, a domain expert can hone in on a set of causal insights that lead to a solution to the root cause of deviations.
REFERENCES - K. Murphy, Machine Learning: A Probabilistic Perspective, MIT Press, 2012.
- M. Schlang et al., “Neural Computation in Steel Industry,” European Control Conference, IEEE, 1999, pp. 2922–2927.
- S. Hamidinejad, F. Kolahan and A. Kokabi, “The Modeling and Process Analysis of Resistance Spot Welding on Galvanized Steel Sheets Used in Car Body Manufacturing,” Materials & Design, Vol. 34, 2012, pp. 759–767.
- S. Kampakis. “Hiring and Managing Data Scientists,” The Decision Maker’s Handbook to Data Science, Springer, 2020, pp. 105–123.
- J. Peters, D. Janzing and B. Schölkopf, Elements of Causal Inference: Foundations and Learning Algorithms, MIT Press, 2017.
MACHINE VISION Machine vision plays an important role in a variety of applications these days. The rapid development of machine-learning (ML) technologies allows for designing and executing predictive models that can analyze very complex data. Due to the commonly available computational capabilities — mainly based on graphical processor units (GPUs) — and mature machine learning libraries, extensive neural network (NN) architectures can be exposed to a huge amount of production image data. This results in significant predictive capabilities to make a precise decision based on complex input image data.
This paper presents an application of convolutional neural network (CNN) architecture for detecting defects on steel surfaces. The proposed approach is based on composite ML architecture containing two independent NNs. Based on input data in the form of a steel surface image, the solution precisely segments the picture showing the locations of probable defects. DEFINITIONMachine vision technology is the set of methods used to automatically extract information from an image.8 The response from an algorithm can have very different forms. It may be basic like a binary classification of the provided image. On the other hand, a machine vision system can return very complex information about an object present on an image, such as position, size, type and orientation. Also, the image is not limited to typical photography. The subject of a machine vision can be a normal photo as well as an x-ray, ultrasound image, infrared image, 3D image and any other possible way of imaging. This makes machine vision a wide area with application possibilities in a variety of industries.
Within this field, there is a combination of technologies, software, hardware, integrated systems and human expert knowledge to solve real-world problems meeting the requirements of industrial automation and similar application areas. The information returned by a system can be used for applications such as automatic inspection and robot and process guidance in industry, for sorting goods based on their appearance, for security monitoring, vehicle guidance, and many others.
Such models can easily be introduced in the steel production management process; for example to detect defect types from production images, to identify scrap type from truck or wagon pictures before unloading or identify the scrap grip contents while preparing baskets, unblock material decisions, identify complex plate pile topology, etc. HISTORYMachine vision has a long and prominent history. It is noteworthy to mention the pioneer paper of David Hubel and Torsten Viesel 1 describing the core response properties of visual cortical neurons. After some years, this led Japanese computer scientist Kunihiko Fukushima to invent the idea of Neocognitron, 2 which can be understood as a prototype of modern CNN architecture. The idea of Neocognitron resulted in a variety of CNN-based architectures solving various problems of machine vision.
ImageNet3,4 is a project and challenge that gave much to the area of CNN application in a machine vision. Their database contains more than 14 million hand-annotated images. Additionally, for at least 1 million of the images, the bounding boxes related to the annotations are also provided. The task is to predict which object from more than 20,000 categories is present on an image. Since 2010, the ImageNet project runs an annual software contest in which software programs compete to correctly classify and detect objects and scenes. Each year, contestants introduce more and more complex NN architectures, which achieve constantly improved results. Fig. 1 shows a plot presenting the results, expressed as an average error rate, achieved in this competition over the years.
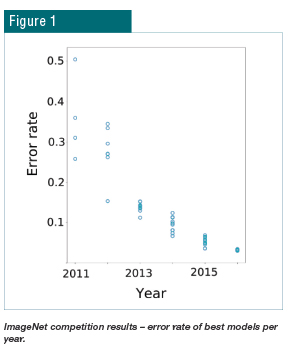 The community can benefit from this project in many ways. First, the database is a trusted source of annotated images and can be used to train new models. Secondly, one can copy the best architectures, which are tested and proved to work very well. What is more, the technique called transfer learning can be applied here. Both the architecture and trained weights can be taken and considered as an initial pre-trained predictive model. In order to incorporate the nature of steel defect pictures, this model should be only retrained on the final data set. TECHNOLOGIESNowadays, since there are much more publicly available data, machine learning and especially neural processing are becoming increasingly important in the area of machine vision. In this approach, the more training data related to a target, the better the results. The libraries supporting applications involving neural networks are also very scalable. Whenever there is a need to increase the number of processed images or to increase the architecture size, it is enough to add another GPU. The next important advantage of this solution is there is no need for expert domain knowledge in the given field. One skilled machine learning engineer can solve problems in a variety of areas. Additionally, one can use amazing libraries to build a neural network on a high level of abstraction without worrying about details or performance.
On the other hand, there are plenty of specialized algorithms in the machine vision field. Using them, one can build from scratch a fully functional machine vision system with significantly less training data available. This includes such methods as morphological operations, multiple filters, edge and shape detection, optical character recognition (OCR), etc. For such approaches, there are also efficient libraries that allow users to use all these methods in a fast and easy way.
Both approaches can also be mixed. One can pre-process and post-process an image using image processing algorithms while the core part will be done using CNN. There are also solutions based on NNs that can be used as a part of traditional processing, e.g., facial recognition. SAMPLE APPLICATIONMachine vision in the steel industry can be used for surface defect detection. It allows us to find defects much faster and more precise than any human being. Within a fraction of a second, a modern solution can analyze hundreds of steel surface pictures and determine whether there is a defect as well as the defect type and the position of it.
To solve a steel surface defect detection problem, a composite approach consisting of two predictive models (see Fig. 2) is proposed. The first one — a classifier — can detect whether there is a defect and which defect type it is. If this model returns positive information, then the image is passed to the second model — a segmentator — which detects the position of the defects.
It is worth mentioning that introducing the classifier part allows a significant reduction of false positives.
In order to build a model that can achieve good results on the relatively small data set,6 transfer learning is applied twice. First, an NN architecture called EfficientNetB0 is used, trained on the ImageNet data set, and slightly customized last layers to adjust architecture to a given problem — classification or segmentation. Then, these models were retrained on a larger database containing the proprietary images with steel defects. At this level, the models are capable of detecting defects on a steel surface, but only like those from this training data. Then transfer learning is used one more time — copying these models and again retraining them on a new set of images. This time an open data set was applied, containing six common magnetic tile defects.6 In the case of the first data set used, there were approximately 50,000 pictures, among which about one-fourth were related to the defects. The second data set contains 1,345 pictures, where almost 400 were related to the magnetic tile defects. All pictures were scaled to a common resolution of 120 × 800 pixels. In order to artificially expand the size of the data set, image augmentation techniques were applied — in particular, rotation, reflection, zooming and blurring. On the top of each picture, the histogram equalization technique was applied. On a separate channel of the picture, the binary bitmap was also provided, containing detected edges reflecting the most important shapes and motifs. Of the pictures, 75% are always for learning and the rest are used for test/validation purposes. The training was carried out in a standard manner by using Keras library with a TensorFlow back end.7,8 In order to avoid overfitting, the loss function calculated on top of the validation data set was monitored. The neural network optimization was stopped when the monitored metric was not improving within 5 epochs. Usually a couple hundred epochs were enough to converge the neural network. The exemplary results can be seen in Figs. 3 and 4. It is noteworthy that the predictive model can provide the qualitative and quantitative description of the defects of various metallurgical natures. The composite design of the network successfully alleviates the false positive ratio. The classifier part of the predictive model has excellent quality metrics of 0.96, 0.95 and 0.97 in terms of accuracy, precision and recall, respectively. The quality of the segmentator expressed as a dice coefficient, which can be interpreted as a pixel-wise agreement between the prediction and the ground truth, is equal to 0.75. Thus the resulting predictive model is robust and reliable.
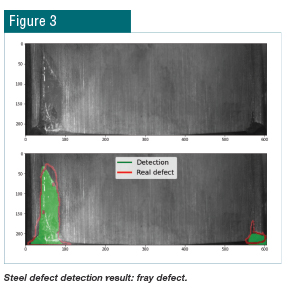 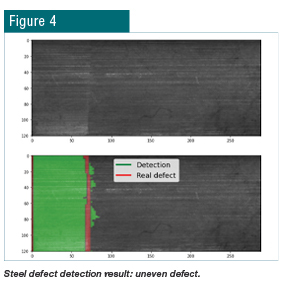 There are also many other applications of machine vision in the steel industry.9 One of them is a measurement of rhombodity and ovality in a continuous casting shop. The machine vision system measures the length of diagonals and, based on the difference between them, decides whether the product can be rolled. The others are the use of OCR to read coil details that are printed on it to determine the path of further processing or vision-guided robotics where the output of the machine vision system is used to determine the movement of robotic arms. SUMMARYMachine vision is still a growing field of computer science; however, it already can be found in many areas of the steel industry. Further deployments can be expected in nearly all processes as the models are becoming better and more reliable. They can efficiently support human employees or even replace them at some level, making the steel production process more automatized, hence faster, safer and cheaper. An application of machine vision paradigms have been shown here in the context of a particular use case, namely surface defect detection. The currently available machine learning tools allow for creating very effective, robust and reliable applications that can be successfully applied in the context of automated recognition of steel surfaces.
REFERENCES - Hubel, D.H., and Wiesel, T.H., “Receptive Fields of Single Neurones in the Cat’s Striate Cortex,” J. Physiol., Vol. 148, No. 3, 1959, pp. 574–591.
- Fukushima, K., “Neocognitron: A Self-Organizing Neural Network Model for a Mechanism of Pattern Recognition Unaffected by Shift in Position,” Biol. Cybernetics, Vol. 36, 1980, pp. 193–202.
- Russakovsky, O.; Deng, J.; Su, H.; Krause, J.; Satheesh, S.; Ma, S.; Huang, Z.; Karpathy, A.; Khosla, A.; Bernstein, M.; Berg, A.C.; and Fei-Fei, L., “ImageNet Large Scale Visual Recognition Challenge,” International Journal of Computer Vision, 2015.
- Wikipedia, ImageNet, 2020.
- Steger, C.; Ulrich, M.; and Wiedemann, C., Machine Vision Algorithms and Applications, Weinheim: Wiley-VCH, 2018.
- Huang, Y.; Qiu, C.; Guo, Y.; Wang, X.; and Yuan, K., “Surface Defect Saliency of Magnetic Tile,” IEEE 14th International Conference on Automation Science and Engineering, 2018.
- Chollet, F., et al., Keras, https://keras.io, 2015.
- Abadi, M., et al., TensorFlow: Large-Scale Machine Learning on Heterogeneous Systems, http://www.tensorflow.org, 2015.
- Mallik, K.; K., J.; and R., K., “Innovative Machine Vision Applications in Steel Industry,” Steel India, 2011.
|