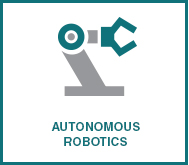 | | Making iron and steel comprises many tasks that require the use of human muscles and minds. Lifting, pulling, grabbing, pushing and deciding are done innumerable times daily to produce and deliver iron and steel products. As technology evolves, more and more of these tasks are being executed by robots. The future will see autonomous robots performing more and more of these tasks. DEFINITIONAutonomy is defined as freedom from external control or influence.1 A robot is a machine capable of carrying out a complex series of actions typically resulting in higher task repeatability and accuracy. Robots require human programming to provide task parameters.
Autonomous robotics allows for prolonged task execution in an operation without human intervention. These robots use sensors to gain information about their environment and perform actions without the explicit direction of a human operator.2 Autonomous robots incorporate functions that differentiate them from traditional robotics.
Examples include: Self-maintenance: A robot senses its internal status and can trigger action to remedy any abnormalities. For example, a mobile robot decides to return to a charging station to charge its own battery. Environmental sensing: Examples of additional sensors may include camera vision systems, lidar (laser radar), temperature sensors, audio sensing, infrared and ultrasound. Decision-making: Instead of following a fixed cycle, an autonomous robot can adapt its actions based on sensed inputs. For example, a self-driving car is able to change lanes to drive around an obstruction in the road.
HISTORYThe first digitally operated and programmable robot, the Unimate, was installed in 1961 to lift hot pieces of metal from a die-casting machine and stack them.
In 1997, the Sojourner rover operated on Mars for 87 days, with much of that time being autonomous operation because of the long delays that direct control would have introduced. The rover relied on a fusion of measurements from inertial sensors, wheel encoders, lidar, and camera for navigation and mapping.
In 2002, a more ubiquitous example of an autonomous robot came with the release of the Roomba by iRobot. It cleans floors without needing to be programmed with the shape or size of the room.
In 2016, Boston Dynamics introduced Spot, a robotic dog that navigates complex and changing terrain using self-determined routes.
TECHNOLOGIES
What differentiates autonomous robots from that which came before comes down to three key technologies that have advanced greatly in recent years: sensors, software and processing power. The sensitivity and resolution of sensors continue to improve. Advanced systems such as lidar allow robots to precisely perceive depth to better define the 3D space they occupy.
While conventional software is still being used in autonomous robots, advanced software that uses artificial intelligence or machine learning, which is better able to make sense of the flood of granular and nuanced data, is becoming more commonplace. Software complexity has risen with the need to fuse data from cameras, radar, infrared, light detection and ranging (lidar), global positioning systems and others in real time.
Lastly, the impact of increased central processing unit (CPU) processing power and the emergence of dedicated application-specific integrated circuit (ASIC) processors has allowed emerging software to make use of improving sensors. ASIC processors are integrated circuit chips customized for a particular use, rather than CPUs, which are intended for general purpose use. The use of this technology increases speed and efficiency of data ingestion. When doubling the resolution of a sensor, the amount of data it produces quadruples, illustrating the increased need for raw computational power. EXAMPLE APPLICATIONSToday, robots are widely used in manufacturing, assembly, packaging, mining, transport, earth and space exploration, surgery, laboratory research, safety, and the mass production of consumer and industrial goods from autonomous helicopters to robot vacuum cleaners.3 These self-reliant robots can move themselves throughout the operation without human assistance and are able to avoid situations that are harmful to themselves, people or property. Autonomous robots are also likely to adapt to changing surroundings.
The most visible and emerging application of autonomous robotics is the in the field of self-driving cars. This has the potential to dramatically reduce road fatalities as robots don’t suffer from distracted driving. With radar, driving is less dependent on weather scenarios — they can see through rain and fog far better than humans. At this point, every major automotive manufacturer is developing in this space.5
Autonomous mobile robots are now commonplace in many warehouses, helping workers to fulfill orders quickly and efficiently.
In the steel industry, autonomous robots have helped increase safety, operation efficiency and process reliability at the caster through the automation of manual tundish operations. Ternium installed a robotic system that uses two robots to automate temperature measurement, sampling, powder application and ladle shroud manipulation. This system was a substantial technological step forward and helped change the daily work experience of Ternium’s employees.6 SUMMARYWhen thinking about the difference between robots and autonomous robots, an easy distinction is the following: robots rely on a repeatable environment and task in order to successfully operate; autonomous robots perceive the world around them dynamically, adjusting to changing conditions while still achieving their objectives. In the iron and steel industries, these advancements allow for the operator to maintain a lower level of exposure to hazards in the area.
REFERENCES Oxford Learner’s Dictionary, https://www.scribbr.com/apa-examples/dictionary. 2. Wikipedia, https://en.wikipedia.org/wiki/Autonomous_robot. 3. “What Are Autonomous Robots?” RobotWorx, https://www.robots.com/articles/what-are-autonomous-robots. 4. A. Davies, “VW’s Robo-Cars Get a Boost From Luminar’s Lidar,” Wired, https://www.wired.com/story/vw-audi-aid-luminar-lidar-self-driving. 5. J. Kaplan, “Here’s Every Company Developing Self-Driving Car Tech at CES 2018,” Digital Trends, 2018, https://www.digitaltrends.com/cars/every-company-developing-self-driving-car-tech-ces-2018/. 6. F. Ramstorfer, L. Martins Demuner, F. Luiz Lourenço, V. Cunha Aranda, V. Sinhorely Oliveira, W. Junior Correa, E. Hernandez Duarte and L. Mascarenhas Fernandes, “Increasing Safety, Operation Efficiency and Process Reliability: Implementation of Robotized Tundish Operations at Ternium Brazil,” AISTech 2019 Conference Proceedings, 2019.
|