Oerlikon Leybold Vacuum Enhances Productivity in Heat Treatment and Metallurgy With Modern Vacuum Systems
06/05/2015 - Innovations in vacuum technology deliver an important contribution to productivity in heat treatment and furnace construction as well as in secondary metallurgy.
In the search for energy efficiency potentials, manufacturers of heat treatment plants increasingly consider the value of modern vacuum systems. For a long time, the top priority was placed on trouble-free operation and reliable production of the required vacuum level. Apart from fulfilling these demands, manufacturers such as Oerlikon Leybold Vacuum have constantly and intensively worked on improving the energy efficiency of their vacuum solutions - with good results.
When developing modern screw vacuum pumps the reduction of energy consumption has been given a high focus - it is now at about the same level of established oil-sealed rotary vane pumps or rotary piston pumps.
Most pumps in the 600 m3 / h class require in a typical furnace operating pressure below 1 mbar an output of approximately 10 kW. Here, the screw pumps of the DRYVAC series of Oerlikon Leybold Vacuum achieved a much lower energy balance in with a reliable performance, due to an optimized rotor design, an innovative drive concept and the installation of a perfectly adapted frequency converter.
The power consumption of DRYVAC DV650 sets new standards for energy consumption of backing pumps and amounts to only 6.9 kW at 1 mbar and is therefore even below that of a comparable rotary vane pump. The built-in frequency converter offers additional energy savings and greater process control. Many process steps do not require the full pumping speed, particularly when operating under rougher pressure ratios, as during carburizing.
In fore-vacuum applications, dry compressing screw pumps have proven themselves even under very rugged conditions. They offer a higher degree of robustness and insensitivity towards dust, particles, and vapors at significantly lower maintenance cost.
In addition to energy savings using modern screw vacuum pumps, similar opportunities arise when using modern Roots pumps or with an optimized operation of rotary vane pumps. In addition, Oerlikon Leybold Vacuum has improved on the established Diffusion pump technology and created a modern and retrofit-able power control unit which offers a reduction of the energy demand of these pumps by up to 30%.
These developments affect the efficiency of modern industrial furnaces: With optimized vacuum systems, the efficiency will be much higher compared to older ovens.
Today, a user should evaluate all of the options that arise due to modern and innovative technology. The power intake of the fore-vacuum system only represents a comparably small part of the overall power consumption of the vacuum furnace. However, over the entire service life of the vacuum furnace, the cost savings can be significant, and an investment makes sense.
Modular Vacuum Systems for secondary metallurgy
In modern steel degassing innovative mechanical pump systems are used instead of energy-intensive steam ejector systems. They enable operators to reduce operating costs and emissions.
The modular concept of Oerlikon Leybold pumps for vacuum technology in steel degassing systems has proven its merits: customers such as Siemens Metals Technologies and Inteco ordered mechanical vacuum systems for steel degassing plants, e.g. for end users in Mexico or China. In order to meet the growing requirements for explosion protection, some of these projects have been supplied with ATEX certified degassing modules.
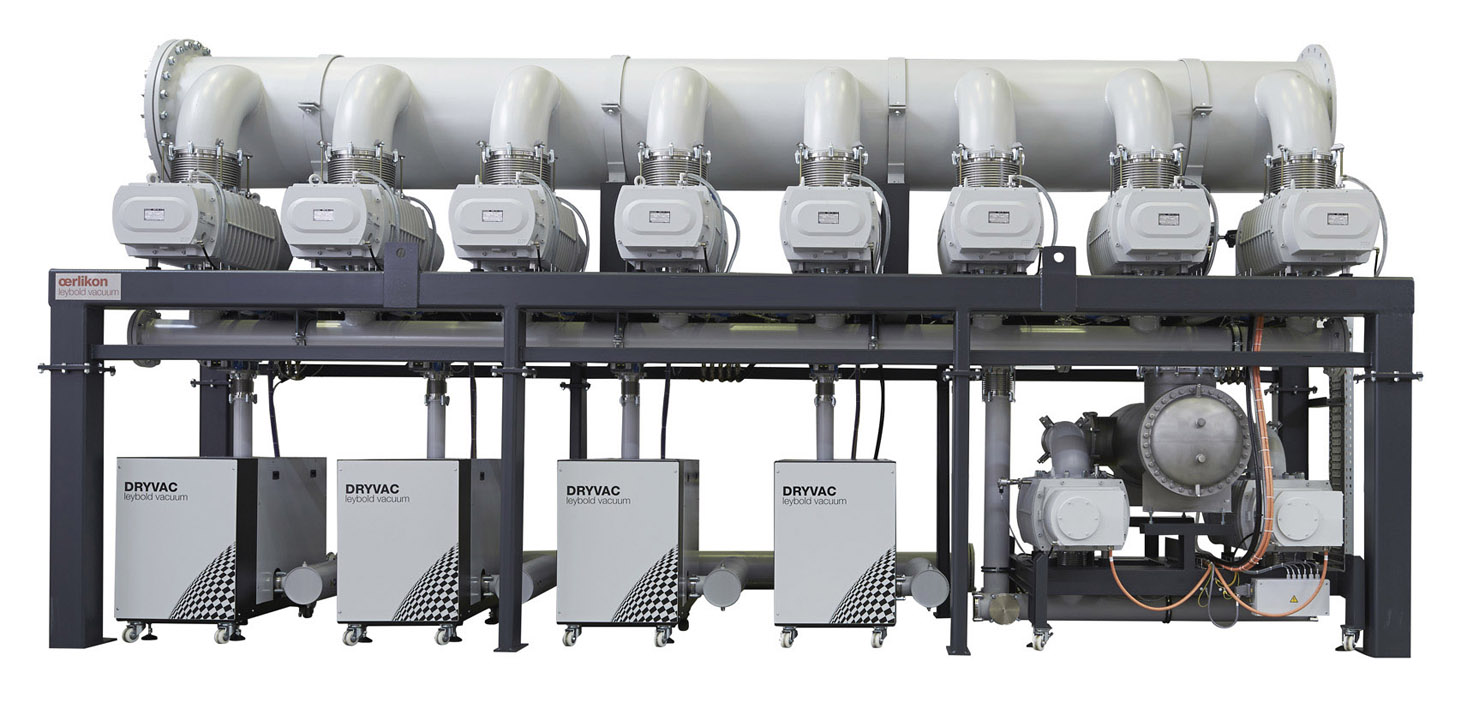
Pictured above: Modular Vacuum System Steel Degassing ATEX from Oerlikon Leybold Vacuum.
Within the modules, Oerlikon Leybold Vacuum only uses two different vacuum pump types, both of which were developed in-house and are manufactured in the Cologne plant in large quantities, also for other applications. These are mainly the Roots pump RUVAC WH7000 and the screw type vacuum pump DRYVAC DV1200. Both types of pumps are the most advanced versions of their pump types, optimized for use in demanding applications. The use of just two types of pumps which are quickly available worldwide, simplifies service and spare parts stock keeping for the end customer.
Modern pump technology is robust, reliable, and environmentally friendly reducing operating costs. Thus, the systems fit exactly to the increasing requirements of steel manufacturers to produce high-quality steel with lower emissions and with a view at costs.
Oerlikon is a leading global technology Group, focusing on providing market-leading technologies and services for surface solutions, manmade fibers manufacturing, drive systems and vacuum pumps and components in growth markets. These cutting-edge technologies benefit customers by improving their product performance, productivity, efficient use of energy and resources, and also by contributing to a more sustainable environment. A Swiss company with over 100 years of tradition, Oerlikon has a global footprint of over 15 500 employees at more than 200 locations in 36 countries and sales of CHF 3.2 billion in 2014. The company invested CHF 121 million in R&D in 2014 and has over 1 300 specialists developing innovative and customer-oriented products and services.