New Side Guide System from Siemens Reduces Hot Strip Mill Maintenance Costs
12/18/2014 - With the newly developed Eco Slide Disc Solution, Siemens Metals Technologies offers operators of hot strip mills a side guide system which can be adapted to nearly all existing entry guides and elongates the lifetime of wear parts up to 10 times compared to conventional wear plates.
The core of the solution consists of wearing discs which are integrated into the entry side guides. After the wear limit has been reached, the discs can be simultaneously round up to eight times, every time offering a new sliding surface. Furthermore, the discs can be turned over to their back face to be used on both sides. This optimizes strip guidance eliminates personnel-intensive replacement processes in the safety zone and reduces the costs of operational wear parts by up to 75 percent. The system can pay for itself within one to two years. Since August 2014, the Eco Slide Discs have been in continuous use at voestalpine Stahl GmbH in Linz, Austria.
Guiding hot strip during the coiling process into marketable coils results in high wear of the down coiler entry side guides. This requires a frequent replacement of the wear plates, sometimes daily, leading to high operational, maintenance and stockpiling costs. In most cases, the changeover is done during the short work roll changing break which takes about ten minutes.
The turnable modules of the Eco Slide Disc system are featuring a robust and maintenance-free design, enabling simultaneous rotation of the wear disks during production. The consequent improvement in strip guidance reduces the risk of damage to the strip edges and additionally substantially increases the life cycle of the wear parts. The risk of strip surface defects due to burning burrs falling off the wear plates can be reduced by continuous rotation of the sliding discs. The exchange of worn out discs can be executed during a maintenance shift, which usually takes place every one to two weeks. There is no need for the repair welding and grinding work performed by many operators on the expensive wearing plates.
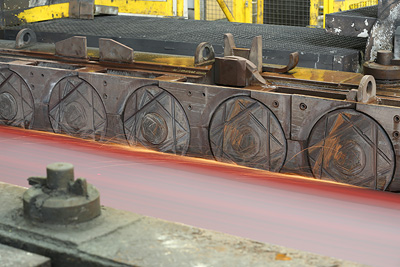
Pictured above: Eco Slide Disks in the hot rolling mill of voestalpine Stahl GmbH in Linz, Austria. At the time the photograph was taken, the disks had been in continuous operation for 14 days. During that time, 3,638 coils with a total length of more than 2,800 kilometers were wound.
Guiding hot strip during the coiling process into marketable coils results in high wear of the down coiler entry side guides. This requires a frequent replacement of the wear plates, sometimes daily, leading to high operational, maintenance and stockpiling costs. In most cases, the changeover is done during the short work roll changing break which takes about ten minutes.
The turnable modules of the Eco Slide Disc system are featuring a robust and maintenance-free design, enabling simultaneous rotation of the wear disks during production. The consequent improvement in strip guidance reduces the risk of damage to the strip edges and additionally substantially increases the life cycle of the wear parts. The risk of strip surface defects due to burning burrs falling off the wear plates can be reduced by continuous rotation of the sliding discs. The exchange of worn out discs can be executed during a maintenance shift, which usually takes place every one to two weeks. There is no need for the repair welding and grinding work performed by many operators on the expensive wearing plates.