Meros Plants from Siemens to Clean Sinter Offgases for Ilva in Italy
02/26/2014 - Italian steel producer Ilva S.p.A. has awarded Siemens Metals Technologies an order to supply four turnkey Meros plants for the two sinter plants in its Taranto steel mill.
The plants will make a substantial contribution toward improving the environmental situation in Taranto. The Meros process developed by Siemens will help to clean all the offgas from the sinter process — totaling more than 2.6 million cubic meters per sinter plant per hour. This will reduce emissions of sulfur dioxide, fine dust, organic compounds, heavy metals and acidic gases to levels significantly below the usual limits in Europe. The first two Meros plants are scheduled to go on stream in April 2015 and the other two will follow in September 2016. The value of the order lies in the mid double-digit million euro range.
In the future, the fine dust emission via the smoke stack of Ilva’s sinter plants in Taranto will be reduced by more than 1,000 tons compared to the legal emission level, which is actually set at 40 micrograms per standard cubic meter. Furthermore, the dioxin emission will come down from the actual emission load of 12 grams per year at the actual limit of 0.4 nanograms I-TEQ per standard cubic meter to a level less than 3 grams per year. The design of the plant is also featuring installations for major sulfur dioxide reduction.
The Ilva steel plant in Taranto belongs to the Riva Group. With an annual production capacity of over eleven million metric tons, it is the largest in Europe and produces around 30 percent of the steel used in Italy. Both sinter plants were modernized and extended by Siemens in 2001, and can produce up to eleven million metric tons of sinter a year. Siemens recently won an order in summer 2013 to equip the sinter plants with two new secondary dedusting systems.
The Meros plants will replace the existing outdated MEEP electrostatic precipitators, which can only remove dust. The new units will be installed and integrated into the offgas system of the sinter plants during ongoing operation, which will only require brief shutdown times. The Meros process involves injecting and finely distributing adsorption and desulfurizing agents, such as activated carbon and sodium bicarbonate, into the flow of offgas. This efficiently binds and removes heavy metals, harmful and hazardous organic components, as well as sulfur dioxide and other acidic gases. The use of sodium bicarbonate to reduce the amount of sulfur dioxide also eliminates the need for a conditioning reactor. The process is water-free, which avoids steam plumes coming from the smoke stack. The dust particles are deposited in a specially developed, energy-efficient bag filter, which is suitable for temperatures of up to 250°C and very low cleaning pressures. The greater part of the dust removed by the precipitator is recycled back into the flow of offgas to further optimize the efficiency and cost-effectiveness of the gas purification process. Any remaining unutilized additives are then once more in contact with the offgas, so that they are finally almost completely utilized. There is also considerably less discharged residue when sodium bicarbonate is used instead of slaked lime. The process automation system ensures stable operation, even when there are considerable fluctuations in the volume and composition of the offgas. Emission limits can therefore be observed at all times.
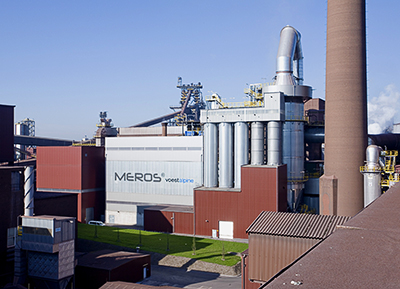
Italian steel producer Ilva S.p.A. has awarded Siemens Metals Technologies
In the future, the fine dust emission via the smoke stack of Ilva’s sinter plants in Taranto will be reduced by more than 1,000 tons compared to the legal emission level, which is actually set at 40 micrograms per standard cubic meter. Furthermore, the dioxin emission will come down from the actual emission load of 12 grams per year at the actual limit of 0.4 nanograms I-TEQ per standard cubic meter to a level less than 3 grams per year. The design of the plant is also featuring installations for major sulfur dioxide reduction.
The Ilva steel plant in Taranto belongs to the Riva Group. With an annual production capacity of over eleven million metric tons, it is the largest in Europe and produces around 30 percent of the steel used in Italy. Both sinter plants were modernized and extended by Siemens in 2001, and can produce up to eleven million metric tons of sinter a year. Siemens recently won an order in summer 2013 to equip the sinter plants with two new secondary dedusting systems.
The Meros plants will replace the existing outdated MEEP electrostatic precipitators, which can only remove dust. The new units will be installed and integrated into the offgas system of the sinter plants during ongoing operation, which will only require brief shutdown times. The Meros process involves injecting and finely distributing adsorption and desulfurizing agents, such as activated carbon and sodium bicarbonate, into the flow of offgas. This efficiently binds and removes heavy metals, harmful and hazardous organic components, as well as sulfur dioxide and other acidic gases. The use of sodium bicarbonate to reduce the amount of sulfur dioxide also eliminates the need for a conditioning reactor. The process is water-free, which avoids steam plumes coming from the smoke stack. The dust particles are deposited in a specially developed, energy-efficient bag filter, which is suitable for temperatures of up to 250°C and very low cleaning pressures. The greater part of the dust removed by the precipitator is recycled back into the flow of offgas to further optimize the efficiency and cost-effectiveness of the gas purification process. Any remaining unutilized additives are then once more in contact with the offgas, so that they are finally almost completely utilized. There is also considerably less discharged residue when sodium bicarbonate is used instead of slaked lime. The process automation system ensures stable operation, even when there are considerable fluctuations in the volume and composition of the offgas. Emission limits can therefore be observed at all times.
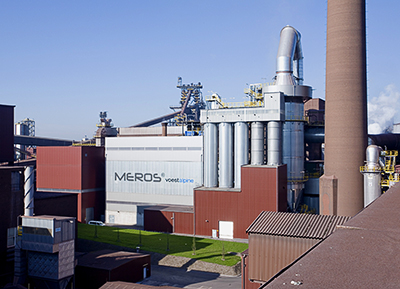
Italian steel producer Ilva S.p.A. has awarded Siemens Metals Technologies
an order to supply four turnkey Meros plants for the two sinter plants in its Taranto steel mill.