Continuous Slab Caster from Siemens Receives FAC from Maanshan
10/22/2014 - Siemens Metals Technologies received the final acceptance certificate for a continuous slab casting machine with an annual capacity of 2.4 million metric tons from China's Maanshan Iron & Steel Corp.
The two-strand caster CCM 3 was set up in the company's BOF steelmaking shop in Maanshan. A large number of grades for different applications can be produced, mainly for the construction and automotive industries, but also for the oil and gas and electric sector. A series of technology packages ensures high slab interior and surface quality.
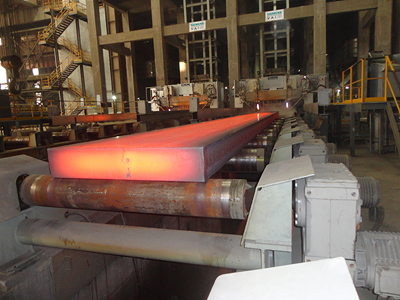
Pictured above: Continuous slab casting machine CCM3 from Siemens
in the BOF steel making shop of Maanshan Iron & Steel
in Maanshan, China.
Maanshan is a leading steel producer in China. The company has its headquarters in Maanshan, Anhui province, in the south-east of the country, and produced around 18.8 million metric tons of steel in 2013. The new two-strand continuous slab caster from Siemens features a straight cassette-type Smart Mold and, with a machine radius of ten meters, has a metallurgical length of 34.5 meters. A total of 2.4 million metric tons of slabs with widths between 950 and 1,600 millimeters and a thickness of 230 millimeters can be cast. Casting speed is 1.8 meters per minute. The casting plant is designed for a wide range of steel grades, including ultralow to medium carbon steels, structural steel, micro-alloyed and peritectic steels, silicon grades and also high-strength, low-alloyed, pipeline and tinplate grades.
Siemens handled the project management, design and manufacturing of key components like molds and oscillators, and executed manufacturing, erection and commissioning supervision for the entire casting plant .The technology packages from Siemens are essential to the interior and surface quality of the slabs produced. These include LevCon mold level control, DynaWidth for automatic adjustment of slab width and Mold Expert breakout prediction. The position of final solidification of the slab can be determined with considerable accuracy, and the roller gap can be controlled precisely, with the aid of Dynacs 3D and DynaGap Soft Reduction 3D. This results in a high internal slab quality. Together with eight-zone spray mist cooling and internally-cooled I-Star rollers, in combination with the Dynacs 3D dynamic secondary cooling model a high quality on the slab surface is ensured.
The scope of supply also included the complete basic (level 1) and process automation (level 2), an in-line electromagnetic stirrer, the torch cutting machine, the deburrer and a marking machine as well as weighing and transfer equipment. This was supplemented by customer training and also monitoring of installation and commissioning work.
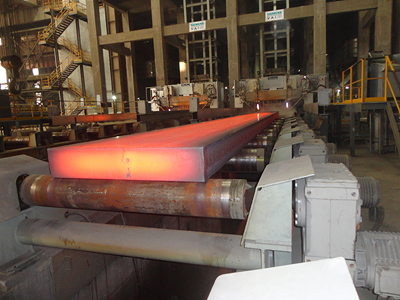
Pictured above: Continuous slab casting machine CCM3 from Siemens
in the BOF steel making shop of Maanshan Iron & Steel
in Maanshan, China.
Maanshan is a leading steel producer in China. The company has its headquarters in Maanshan, Anhui province, in the south-east of the country, and produced around 18.8 million metric tons of steel in 2013. The new two-strand continuous slab caster from Siemens features a straight cassette-type Smart Mold and, with a machine radius of ten meters, has a metallurgical length of 34.5 meters. A total of 2.4 million metric tons of slabs with widths between 950 and 1,600 millimeters and a thickness of 230 millimeters can be cast. Casting speed is 1.8 meters per minute. The casting plant is designed for a wide range of steel grades, including ultralow to medium carbon steels, structural steel, micro-alloyed and peritectic steels, silicon grades and also high-strength, low-alloyed, pipeline and tinplate grades.
Siemens handled the project management, design and manufacturing of key components like molds and oscillators, and executed manufacturing, erection and commissioning supervision for the entire casting plant .The technology packages from Siemens are essential to the interior and surface quality of the slabs produced. These include LevCon mold level control, DynaWidth for automatic adjustment of slab width and Mold Expert breakout prediction. The position of final solidification of the slab can be determined with considerable accuracy, and the roller gap can be controlled precisely, with the aid of Dynacs 3D and DynaGap Soft Reduction 3D. This results in a high internal slab quality. Together with eight-zone spray mist cooling and internally-cooled I-Star rollers, in combination with the Dynacs 3D dynamic secondary cooling model a high quality on the slab surface is ensured.
The scope of supply also included the complete basic (level 1) and process automation (level 2), an in-line electromagnetic stirrer, the torch cutting machine, the deburrer and a marking machine as well as weighing and transfer equipment. This was supplemented by customer training and also monitoring of installation and commissioning work.