ArcelorMittal Ostrava Modernizing Blast Furnace Hot Stoves
10/03/2014 - ArcelorMittal Ostrava is modernizing three hot-blast stoves used for the heating of air blown to its blast furnaces.
The new hot-blast stoves will increase the temperature of hot air by 100°C, thus not only reducing the volume of burned coke but also emissions of carbon oxides. The project is worth 400 million crowns (US$18.4 million).
“I am very glad that within a short period of time I can announce another important investment into modernization of production in the company in spite of difficult situation faced by the industry. After commissioning the modernized continuous steel caster last year, this year we are reconstructing the equipment used for hot metal production,” said Tapas Rajderkar, the CEO of ArcelorMittal Ostrava.
The modernization consists of the complete replacement of internal equipment and refractory brick of the hot-blast stoves. The modernization will not only bring economic savings but also lower the emissions of carbon oxides, which will have a positive impact on the environment.
The construction is delivered by a German company Paul Wurth Refractory & Engineering GmbH. The complete reconstruction of the equipment is carried out under full operation. The beginning of the next year will see commissioning of two new hot-blast stoves and the modernization of the third one will be completed by January 2016.
A hot-blast stove and its function
“I am very glad that within a short period of time I can announce another important investment into modernization of production in the company in spite of difficult situation faced by the industry. After commissioning the modernized continuous steel caster last year, this year we are reconstructing the equipment used for hot metal production,” said Tapas Rajderkar, the CEO of ArcelorMittal Ostrava.
The modernization consists of the complete replacement of internal equipment and refractory brick of the hot-blast stoves. The modernization will not only bring economic savings but also lower the emissions of carbon oxides, which will have a positive impact on the environment.
The construction is delivered by a German company Paul Wurth Refractory & Engineering GmbH. The complete reconstruction of the equipment is carried out under full operation. The beginning of the next year will see commissioning of two new hot-blast stoves and the modernization of the third one will be completed by January 2016.
A hot-blast stove and its function
- A hot-blast stove is an essential piece of equipment for hot metal production
- Its structure has a cylindrical shape with a copula at the top and its height is approximately 35 to 40 meters. Its main function is to heat the air blown to the blast furnace. Increased temperature of air blown to the blast furnace leads to a partially reduced consumption of carbon (coke).
- In order to ensure continuous production of hot air it is necessary to make a serial connection of several hot-blast stoves which then work alternately. The refractory lining is always heated up by burning of blast furnace gas and after heating to the required temperature the lining transfers the heat to the flow of cold air which is heated from the hot lining and blown to the blast furnace.
- This equipment was patented by a native Londoner Edward Alfred Cowper (1819–1893) in 1856. However, in metallurgical production it functions on the same principle till today. Because of the name of the inventor, the hot blast-stove may sometimes be called the Cowper stove.
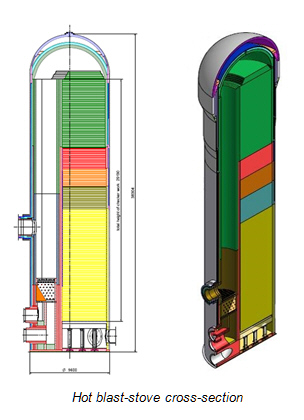