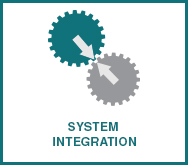 | | System integration can be considered the fabric tying information, control and automation systems together. As digital transformation moves forward in the steel industry, the ability to move data in, out and through systems will require novel concepts and methods. DEFINITIONThe two words “system integration” sound natural together, although in reality the phrase is somewhat superfluous. According to Merriam-Webster’s online dictionary, a system is defined as: “a regularly interacting or interdependent group of items forming a unified whole, such as a group of devices or artificial objects or an organization forming a network especially for distributing something or serving a common purpose.”
Furthermore, integration might be considered a substantive form of the verb integrate. Merriam-Webster provides this for the definition of integrate: “(1) to form, coordinate, or blend into a functioning or unified whole, (2a) to incorporate into a larger unit, (2b) to unite with something else.”
Both words have in their definition the concept of a unified whole, hence the redundancy. The definition of system integration in the context of the digital transformation of the steel industry is the act of connecting all the sources, stores, and processors of data for the whole of steel mill production from dirt to alloyed iron-carbide. Digital transformation needs data to grow. When multiple subsystems are properly defined and connected, not only does the ability to analyze available data increase, but actuators can be commanded to implement more effective operation. System integration allows the intelligence from data analysis to be used in a more productive manner. HISTORYIt is difficult to say when automation and control systems really took hold in the steel industry. Magnetic logic and analog regulation had been available around the time of the vacuum tube invention. Although they provided automated control, their application is not necessarily considered part of an integrated control system. The advent of the industrial computer in the 1960s and its application to steel production facilities could be considered the first integrated system. The central processing unit (CPU) was “centrally” located to reduce the length of input and output connections in the form of discrete wires to sensors, actuators, pushbuttons and lights. There were lots of long wires.
Eventually, engineers developed a method to transceive more than one signal on a wire at a time. The birth of the field network actually caused a subtle “dis-integration” or segregation of the control system. With the ability to communicate more information over a wire, the processing load could now be distributed based on location or functionality of the controlled equipment. The centralized GEPAC 4000 series, Honeywell’s Big Blue, and VAX computers were soon augmented with newly developed programmable logic controllers (PLC) using vendor-specific field networks for aggregation of sensors and actuators. Initially, the communication between these PLCs was sparse to none. They were operating independently with small bandwidth connections to the central computer(s). The combination of CPUs and distributed PLCs were the operational technology of the day.
In parallel with the changes in the mill motor and computer rooms, the business and enterprise side of larger steel facilities were experiencing their own evolution in computerization. Large corporate-level data centers were connected remotely to business unit and enterprise-level terminals using telephone lines and long-haul modem technology of the day. Eventually, as the availability and practicality of the personal computer advanced, the remote terminals connected to large mainframes were supplanted with desktop personal computers, although they were still connected together with phone lines and long-haul modems. That was the informational technology of the day. TECHNOLOGIESTECHNOLOGICAL FRAMEWORK Present systems are somewhat reminiscent of those from the past. The basic components are still there. To help manage these systems, they are often associated with system architectural levels. The levels were created, to a certain degree, with respect to the type of work performed, volume of data, and communication latency or cycle time at each level. Fig. 1 represents this concept. Surprisingly, the equipment/technology applied at each level provides features that maximize the efficiency of the work performed, transfer of data and cycle time. The effectiveness of horizontal communication, within the architectural level, exceeds the ability to share information vertically by design.
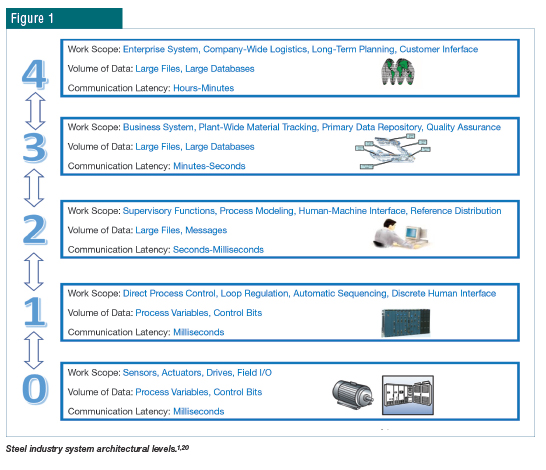 Digital transformation requires information from all the levels. Although there is segregation of equipment and processes between each level, the separation provides some benefits to safe and effective acquisition of data. The logical separation between the levels enables security procedures to authenticate access to data sources and critical processes. At the levels close to the physical steel process, there are thousands of signals collected at millisecond rates. From the lower levels, edge processing and compression for the unique type of data at any particular level reduces storage and bandwidth requirements before the transfer to data stores.
There is also intangible segregation in systems imposed by management philosophy. Many steel producers employing the system level architecture assign levels 3 and 4 to the information technology (IT) realm while levels 0, 1 and 2 are under the purview of operational technology (OT). These groups are from different schools of thought related to the integration of equipment and data, whereby digital transformation will be a disrupter.
SUPPORTIVE TECHNOLOGY At each level, the work scope or processing requirements are similar. This is part of what defines a level. Unfortunately, the equipment and communication method within the level may not share the same similarity. This could be due to growth, obsolescence, added functionality or new ownership strategy. As new equipment and communication methods are added or replaced, there is a need to integrate within the same level and potentially a level above or below. Historical differences in vendor philosophy have led to difficulty in the integration of new equipment.
The evolution of ethernet technology along with standardized protocols have been very beneficial to industrial system integration. Ethernet is a medium upon which many different communication protocols propagate. The different protocols can coexist on the same twisted pair, fiber or radio wave concurrently. All of the protocols can share the ethernet medium to the limits of available bandwidth.
The perception of non-deterministic communication in older ethernet networks has diminished with availability of increased bandwidth and real-time ethernet protocols. Time-synchronized networks down to microseconds are now being implemented.
The Internet of Things has progressed to industrial I/O, sensor and equipment vendors. Their market increases when more users can plug in their products. Vendor proprietary networks have moved toward industry-standard media with published industry-wide protocols. Industrial system providers have also developed gateways3 for older communication technologies using open standards: Open Platform Communication United Architecture (OPC-UA). 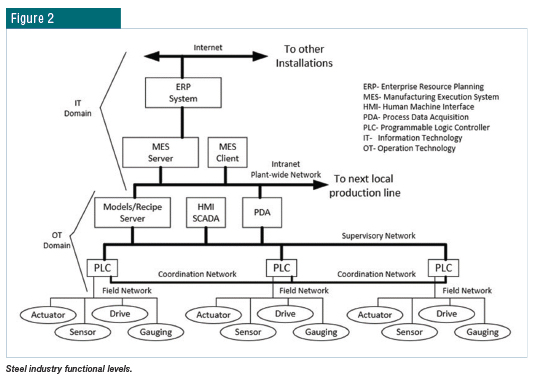
EXAMPLE APPLICATIONSMyriad steel producers and processors all employ some form of automation equipment networked together. At the very least there is a level 0 (see Fig. 1) and some form of communication with the equipment. The size of the installation will determine the quantity and complexity of the applied system architectural levels.
Fig. 2 shows a mythical steel finishing complex integrated into a larger plant with other remote installations. This may not look like a typical mill installation hierarchy, however there are probably a few similarities. The type of equipment and software at each level are purposely designed for maximum effectiveness at that level. That could mean low-latency-low-volume networks to high-volume-streaming networks and environmentally hardened PLCs to air-conditioned server farms. What is not shown are the functional data paths and security devices in the networks at each of the levels. Knowledge of this is key to effective data flow for digital transformation.
The steel industry has typically been an early adopter to new technology. Looking toward the future, what will systems look like when every device has a 5G SIM card installed with access to a private cell network?
REFERENCES - Automation Systems and Integration, Part 1: Framework and Functional Model, ISO-15746-1:2015.
- Enterprise - Control System Integration, Part 2: Object Attributes, ANSI-ISA 95.02-2001.
- Buscaratto, Otavio, et al., “System Integration Between PLCs and IIOT Devices,” COBISA-Congresso Brasileiro de Instrumentacao, Sistemas e Automacao, May 2019.
|