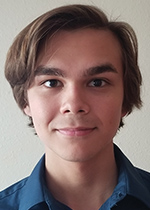
This summer, I was an intern at Cleveland-Cliffs Cleveland Works LLC, Cleveland, Ohio, USA. Working as a metallurgical engineer in their quality department, I had the opportunity to perform elemental analysis of samples using spectroscopy, calibrate analytical instruments, and write standard operating procedures (SOPs). This internship was a cultivating and exciting experience — both as a materials science student and as a future steel professional.
My main project oversaw the performance of elemental analyzation instruments: the x-ray fluorescence (XRF), optical emission spectroscopy (OES) and a carbon/sulfur analyzer. I calibrated these instruments by running standards and adjusting so that the instruments consistently and accurately display elemental compositions. I especially focused on the XRF, in which methods had to be developed for samples in each stage of the steel production process. This involved setting up which elements to look for and running trials to determine how long each element should be scanned.I also wrote and updated various SOPs. As new equipment and tasks are created, it’s important that new SOPs are made so that operators always have a procedure to reference. This is especially important in areas that are continually operating and where help isn’t immediately available. Updating existing SOPs is another important task, since equipment can get updated without it being reflected in the SOP. I loved this aspect of the job because it gave me a porthole into so many different operations. I had the chance to work many different instruments and machinery that have niche responsibilities in the quality department.In my time at Cleveland-Cliffs Cleveland Works LLC, I was continually impressed with the great lengths they took to ensure safety and promote production efficiency. The safety minded work culture was transparent in the policies and the workforce. Learning from this mindset has been an invaluable part of my internship experience. The dedication and team-focused attitude that is necessary in such a potentially dangerous environment also rubbed off on me. In my contributions to the steel community, I felt welcomed into the steel making family.
As an intern at one of the largest flat-rolled steel producers in North America, I had a chance to learn so much about the steel production process. Over the course of several tours, and countless visits to various parts of the plant, I had the opportunity to witness the relationship between sectors as raw iron transforms into specialized steel on a massive scale.
I’d like to extend a wholehearted thank you to AIST and Cleveland-Cliffs. AIST did a great job putting me in network for this opportunity, and Cleveland-Cliffs has done nothing but help me grow with hands on experience. I can tell this internship will lead to promising avenues in my career as a future engineer and steelmaker.