2024 Steel Intern Scholarships
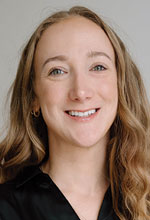
Brooke L. Clark
This summer I had the privilege and opportunity to intern with United States Steel Corporation in Fairfield, Ala., USA, under the guidance of Rudolf Moravec. My internship was based at their FTSO (Fairfield Tubular Steelmaking Operation) location, where steel is melted, refined and cast into blooms which are then shipped to the pipe mill to be made into seamless pipe. Here my focus was casting, but I had the great experience of following the steelmaking process from start to finish. This experience enhanced my knowledge of steelmaking and intensified my passion for the steel industry.
During my time at USS FTSO, I was able to be a part of many different projects. To start any project, safety must come first. While conducting hands-on measurements or simply recording notes while observing, you must pay attention to your surroundings and ensure you are wearing the proper personal protective equipment. While following the safety standard, I was able to successfully finish any task put before me.
My internship began with learning the process flow of steelmaking. The first couple days I followed the ladle from the electric arc furnace to the ladle metallurgy furnace, then to the vacuum tank degasser, and finally to the caster. The first project I worked on and continued to add data to over the summer dealt with mold powder. Mold powder is crucial; without this the steel lacks protection from oxidation. Mold powder also aids in heat transfer and acts as a lubrication in the mold. This showed a “simple” powder wasn’t truly simple. To measure the mold powder, a twisted rod of steel and aluminum is inserted from the top of the mold. Aluminum on the rod is melted by the liquid slag, but mold powder will not melt the aluminum or the steel. Conducting these measurements regularly guarantees the correct amount of mold powder is being fed into the mold.
Additionally, during my time with U. S. Steel, I used the Vuhz system to measure the steel meniscus, analyzed nitrogen pickup and argon flow, gained knowledge on reasons for breakouts, measured camber, and recorded temperatures of blooms exiting the caster versus temperature at the end of the cooling bed.
I am extremely grateful to AIST and U. S. Steel for granting me this opportunity. The amount of knowledge, skills and professional development I gained from this experience is unmatched. I am eager to return to classes this fall with a higher understanding of the steelmaking process and continue following my desire to work within the steel industry.