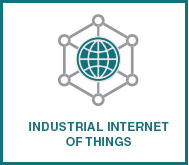 | | The Industrial Internet of Things describes the use of the Internet of Things in multiple industries, such as manufacturing (Industry 4.0), logistics, transportation, energy, mining and metals, and other industrial sectors.
The Industrial Internet of Things (IIoT) covers, the same way as the Internet of Things (IoT), many use cases and applications.
IIoT focuses on optimizing operational efficiency and maintenance and plays an important role in the integration of information technology (IT) and operational technology (OT). It provides many opportunities for automation optimization, smart manufacturing and asset performance management. IIoT is a new way to provide services to customers and the establishment of new revenue with an on-demand service model.1
IIoT is evolving toward the next generation of tactical and strategical IoT/IIoT, which will bring together hyperconnectivity, edge computing, distributed ledger technologies (DLTs) and artificial intelligence (AI). In that sense, IIoT applications are applying AI methods, such as machine learning (ML) and neural networks (NNs), to optimize the processing of information. IIoT incorporates the integration of robotic devices, drones, autonomous vehicles, augmented and virtual reality (AR/VR) and digital twins, and digital assistants. These applications will prompt new products, services and experiences in the industry that offer many benefits to the manufacturing industries, customers and the entire supply chain; this is a more mature goal of industrial digital transformation. THE INDUSTRIAL INTERNET OF THINGS – AN OVERVIEWIoT refers to the set of devices and systems that interconnect real-world sensors and actuators to the internet. IIoT leverages IoT in a context of industrial environment and transformation.
IIoT is a network of interconnected computing devices embedded in physical objects. The purpose is to collect and exchange data, analyze said data, and apply the results to the business context, creating operational savings and improving quality and efficiency.
The data collected from these interconnected devices are used in a variety of ways, all of which can lead to some form of operational transformation.
For example, the data may be analyzed to find problems with inefficient processes. It may provide real-time visibility of the products being processed. It may also be used to predict impending failure or breakdowns of industrial machinery. The basic technologies of IIoT solutions vary by application, but they can generally be divided into three areas: Front-end edge devices that collect data or control processes. Connectivity technology used to transfer data to the processing systems. IIoT platforms that can analyze data and make decisions.
FRONT-END EDGE DEVICES Sensor data is the bulk of IIoT, so the hardware used to collect data is a key part of the system. Front-end devices (such as sensors and control devices) are responsible for collecting and processing continuous streams of data. Only when the IIoT devices used are reliable, consistent and accurate is it possible to obtain a return on investment.
Many industrial environments already have data collection processes. In this case, since data collection already exists, the complexity of adding IIoT data collection is reduced to the level of finding ways to connect to the existing data collection networks.
Without these data collection instances in place, new sensors must be installed.
What hardware is needed to make the required measurements?
Choosing a sensor is not easy. There are mechanical and electrical considerations. For example, if there is a hydraulic oil pipe and the temperature of the cooling fluid flowing from one area to another needs to be measured, it is necessary to determine how the sensor mechanically works.
Will the sensor be connected to the pipe externally, or will it be inserted directly into the pipe through a cut or hole? What type of sensor will it be? How will it be installed, wired and powered?
Designing and implementing sensor technology will soon become a big issue — installing and maintaining them, another. There are many packaged sensor solutions available. The more easy to use, reliable and maintainable they are, the more expensive they are. The solution must take into account future scalability.
CONNECTIVITY AND COMMUNICATIONS TECHNOLOGY Once the data is collected, a transmission mode to the cloud or local system is needed, and the IIoT system needs a way to receive commands from the cloud or local system.
Many IoT solutions rely on wireless technology. Although much of the discussion around IoT device connectivity focuses on wireless connections, wired systems are not uncommon. If the use case supports a wired connection, it may be a cheaper option as it is usually more reliable.
Existing protocols, such as hypertext transfer protocol (HTTP), have an important place for many devices. Even an 8-bit controller can create simple “get” and “post” requests and HTTP provides an important unified (and uniform) connectivity. However, the overhead of HTTP and some other traditional internet protocols can be an issue for two main reasons. First, the memory size of the program can be an issue on small devices. However, the bigger issue is the power requirement. In order to meet these requirements, a simple, binary protocol is needed. The ability to cross firewalls is also required. In addition, there are devices that connect directly and those that connect via gateways. These devices potentially require two protocols: one to connect to the gateway, and then another from the gateway to the cloud.
Finally, there is a requirement for the IIoT architecture to support transport and protocol bridging, offering a binary protocol to the device, but allow an HTTP-based application programming interface (API) to control the device. The following are some communication models between devices and the internet or to a gateway: Direct Ethernet or Wi-Fi connectivity using transmission control protocol (TCP) or user datagram protocol (UDP). Wi-Fi is a local area network (LAN) that provides internet access within a limited range, so it can be used for IIoT applications running in the local environment. Bluetooth. Bluetooth is a short-range technology that is easy to use, but unless the endpoint is used in the same room (or within a couple of meters) of the access point, Bluetooth will not work. In an IIoT environment, Bluetooth can work well if sensors are almost evenly distributed throughout the area. 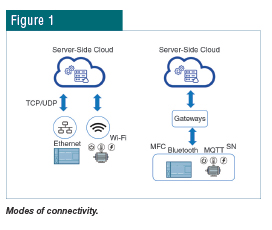 Mesh radio networks. Mesh topology is a type of network where all nodes collaborate to distribute data. Mesh technologies are both powerful and scalable, but their network latency is longer than other wireless technologies. With proper planning, mesh networks may be a good way to obtain wide-area, energy-efficient coverage, but they do not always provide reliable connections.3
Fig. 1 illustrates the two major modes of connectivity.
IIoT PLATFORMS IIoT software is needed to analyze the collected and transmitted data. The software can also make decisions, and in some cases, push commands back to controls at the edges. This supporting software is often referred to as an IIoT platform, connecting edge hardware, access points and data networks to other parts of the value chain, usually end-user applications. It handles ongoing management tasks and data visualization. The IIoT platform is the middle layer between the data collected at the edges and user-facing Software as a Service (SaaS) or mobile applications. The overall requirements of an IIoT platform can be summarized into following key categories: Device management: The ability to disconnect devices. The ability to update the software on a device. Updating security credentials. Remotely reconfiguring Wi-Fi, general packet radio service (GPRS) or network parameters.
Scalability. Any server-side architecture would ideally be highly scalable and be able to support many devices all constantly sending, receiving and acting on data. Security. IoT devices are often collecting sensitive process and production data, and by their nature are bringing the real world onto the internet and vice versa. This brings three categories of risks: Risks that are inherent in any internet system, but that production or IIoT users may not be aware of. Specific risks that are unique to IIoT devices. Safety to ensure no harm is caused by, for instance, misusing actuators.
Predictive analysis applications. Predictive analysis is a branch of advanced analysis that is used mainly to predict uncertain future events. Predictive analysis uses statistics, modeling, data mining, artificial intelligence and machine-learning language to process the current data set provided as instructions and predict future events. By using historical data and transaction data patterns, in addition to exploring opportunities for future needs, risks can also be identified. Using predictive analytics, companies can effectively interpret the available data for their benefit.4
A REFERENCE ARCHITECTURE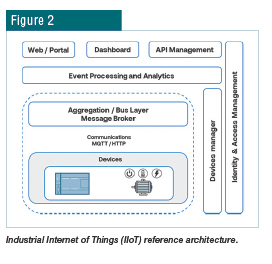 The reference architecture of an IIoT platform in Fig. 2 consists of a set of components. The component layers can be realized by means of specific technologies. There are also some cross-cutting/vertical layers such as access/identity management.2 USE CASE: IOT IN METALS INDUSTRY The following use case is a holistic solution for the continuous sensing, accessing, monitoring, detecting and predicting occurrence of failure events before they happen to support the maintenance planning and the reduction of production downtime in the metals industry. The solution consumes high-frequency time series data and enriches the data pipelines with statistical features and waveform features derived from production variables and determines multi-variate, temporal patterns that are anomalous in the context of the target events, as well as predictive for these events. The system also leverages advanced machine learning to determine the major contributing variables to the anomalies and events, which helps operators diagnose the issues and make operational changes to reduce occurrences.
The main objective of such a system is to reduce downtime and improve asset availability by using data collected for the implementation of AI predictive maintenance models. As part of the solution, an AI platform is implemented to enable the near-real-time collection, unification and smart orchestration of sensor data from the production plant using the digital data factory. The general purpose of the digital data factory is to set up the most convenient and secure way for applications to consume data through a generic API. As displayed in Fig. 3, the data factory comprises various components, starting with a connector, accessing and exploring data residing in a wide spectrum of data sources within the production plant. The connector is followed by a data pipeline, including components such as data engine, data lake, data warehouse, data dictionary and API.1
The IIoT platform hosts the applications that will sense complex patterns across sensors data, detect anomalies in the plant unit’s behavior and provide relevant warnings to the operators and maintenance personnel.
KEY FEATURES OF THE APPLICATION Anomaly detection: Detect complex anomalies from near-real-time sensor data. Failure prediction: Predict equipment failure in advance with associated probability. Near-real-time data ingestion: Ingest variety of near-real-time data sets (factory data: sensors, failures) besides historical data. Feature importance identification: Uncover component- and sensor-level factors that contribute to the anomalies. Measurable model performance: Validate the model’s output quality using relevant metrics. Iterative learning model feedback: Utilize the knowledge of domain experts to classify results and add annotations.
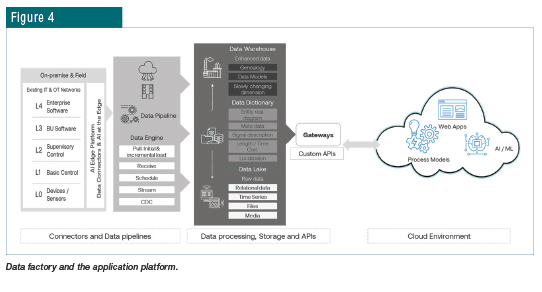 APPLICATION OF THE CONCEPT ON THE SMART MAINTENACE SOLUTIONS Slab casting is the process of producing a solid strand from liquid steel by continuously solidifying the liquid steel as it flows through the casting machine, called the slab caster (see Fig. 5). The resulting product is a slab of steel. This is the main process route of modern steel plants, linking the steelmaking plant with hot rolling mills via the slab caster.
The above-described concept uses a service strategy that handles the complete maintenance activities of a large 300-mm caster and all other standard slab casters, as well as three slab transport and finishing lines. This strategy, called smart maintenance solutions, supports the activities, consolidates a range of digital products and focuses on the maintenance of the asset.
Fig. 5 displays the digital integrated components to implement the smart maintenance solution especially in the field of predictive maintenance. The interconnectivity between the components takes into account the sensor signals on the casting segments, drives and oscillation signals. These signals and the process automation data are collected and linked into the digital data factory and exposed to the application layer hosting simulation tools, prediction and forecasting modules, and decision prescriptive applications. All results of the application layer are bundled, correlated and provided to the integrated maintenance management systems for triggering the actionable activities. Decision and forecast verification is performed using digital equipment and feedback to the system is made. 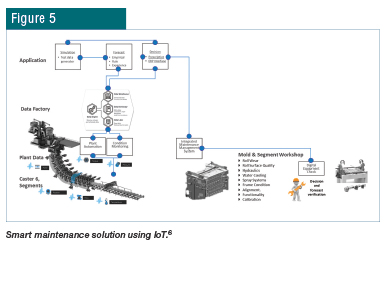 KEY FACTORS FOR A SUCCESSUL IMPLEMENTATION OF IoT PROJECT IN THE METALS INDUSTRY Besides the technical aspects and the selection of the appropriate IoT technologies to implement the IoT project, it is crucial to consider the following key factors contributing to a successful outcome of an IoT project in the metals industry:
Perform a mechanical and operational assessment of the plant unit in consideration to assess the current condition, identify opportunities for improvement, and prioritize subsequent analytic activities. Collaborate with plant operation and maintenance personnel to jointly identify and prioritize the failure modes affecting the availability of the plant unit. Identify, collect, and prepare available data to support physical and AI model implementation. Sequentially and iteratively, implement AI models for anomaly detection on the available data related to the prioritized failure modes. This will allow the observation and monitoring of the improvement of the asset. In addition, this step will provide a baseline for the time-to-failure prediction. Subsequentially implement AI models to predict time to failure for the prioritized failure modes. Integrate operations and maintenance action instructions and rules generation for all failure modes within scope into the production and asset maintenance workflow. Monitor and retrain AI models as needed to maintain performance.
REFERENCES
- F. Adjogble et al., “Holistic Approach of High-Quality Flat Steel Production — Dynamic Production Scheduling in Respect to Process Quality, Control System and Plant Condition,” AISTech 2018 Conference Proceedings, 2018.
- F. Adjogble et al., “Live Process Events Monitoring and Forensics for Product Quality,” AISTech 2019 Conference Proceedings, 2019.
- E. Negri, H. Davari Ardakani, L. Cattaneo, J. Singh, M. Macci and J. Lee, “A Digital Twin-Based Scheduling Framework Including Equipment Health Index and Genetic Algorithms,” 2019.
- P. Girdhar et al., “Machinery Vibration Analysis and Predictive Maintenance,” 2004.
- G. Santillan Martinez et al., “Automatic Generation of a Simulation-Based Digital Twin of an Industrial Process Plant,” 2018.
- C. Häusler, “Smart Maintenance Solution,” https://www.sms-group.com/jp/expertise/technical-service/smart-maintenance.
|